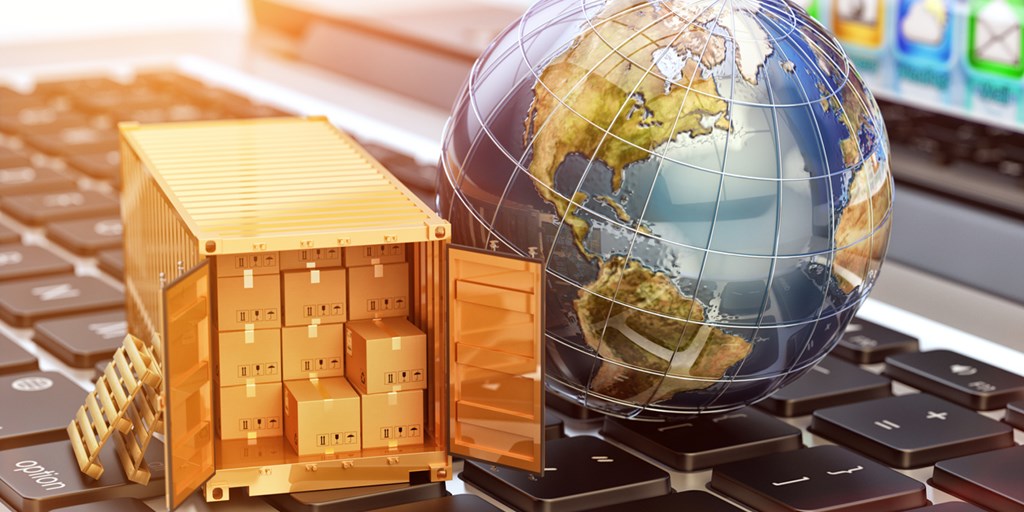
The trend of offshoring manufacturing processes hit its stride in the late 1970s, when large companies such as General Electric (GE) began chasing the idea of lowering costs and maximizing profits by moving operations to cheaper locations. Since then, many other manufacturing companies followed suit at an increasing rate. And as many manufacturing companies found themselves in financial trouble during the recession of the early 2000s, they scrambled to offshore projects in an attempt to stay afloat.
The general thought was that sending operations to emerging markets like China would save on labor costs and material sourcing. But in recent years, advocacy groups like the Reshoring Initiative are pointing out that the theory may be flawed, and that there’s more to it than just surface-level costs.
As the Reshoring Initiative explains it, reshoring is the process of bringing manufacturing and services back to the United States from overseas. This includes projects that require plastic injection molding.
The purpose isn’t just for good PR; rather, there are real financial and environmental benefits that manufacturing companies realize when they decide to reshore, according to the organization. They take the approach of looking at the Total Cost of Ownership (TCO) to give more context to cost analysis of offshoring vs. domestic manufacturing.
Determining TCO
The Reshoring Initiative estimates a 20-30% miscalculation of offshoring costs when companies consider price alone. Instead, companies should be factoring in additional costs like overhead, risk, corporate strategy and many other data points to determine whether or not to offshore operations.
Sound daunting? Don’t worry, they offer a tool called the Total Cost of Ownership Estimator to simplify the process. Recognized by the U.S. Commerce Department, the estimator calculates 30 cost factors from various sources, categorizes costs, provides a five-year TCO forecast and gives a better overall picture of what each source — domestic and international — will cost a company.
Making these comparisons can help give companies a better idea of whether or not reshoring is the right choice.
Additional Benefits
Financial benefits can be objectively determined through the TCO tool, but reshoring goes beyond just the money factor.
Considering that the very premise of offshoring operations involves the movement of goods, materials and services to far away lands, lead time is automatically increased. The parts are packed, trucked to port, shipped, offloaded, and trucked to an end location, and that takes quite a bit of time. Aside from that, if customer demands require a pivot or adjustment, those changes can be implemented and put in market much quicker from a localized supplier.
There are risks associated with products made overseas that can be mitigated through reshoring. Quality control and consistency can be supervised closely, and there are employee safety regulations in place in the United States that may not exist in some nations.
There are minimal intellectual property and compliance risks, and the process is much less cumbersome in terms of physically packing, moving, filling out documentation, taxes, etc. that is involved with manufacturing overseas.
The “Made in America” claim goes far with good public image and trust, as well. U.S. consumers tend to trust products more if they were made domestically. In fact, 80 percent prefer products made in America, and 60 percent said that they’d be willing to pay 10 percent more for a product that was made in America, according to a report by Standard Textile.
Beyond the individual company benefits, manufacturing in the United States is good for the country as a whole. It helps to balance the trade deficit, creates job opportunities and keeps the U.S. competitive in manufacturing innovation. Furthermore, it promotes manufacturing as a growth career for skilled workers.
Likewise, the population is increasingly leaning more toward American-made products in an effort to offset pollution and negative environmental impact. One of the most dramatic benefits of reshoring is its impact on the environment. Long-distance transport and manufacturing in underregulated countries contribute to increased carbon emissions and pollution.
The combination of individual company advantages, benefits to the country, and environmental protections are all compelling reasons to consider reshoring manufacturing operations, including plastic injection molding projects.
Let's Talk
If you’re considering reshoring your plastic injection molding processes, contact Thogus to talk with one of our experts about the process. We can help you determine the next steps and what to expect.
Experience the Thogus Difference
Connect with us today to discuss your project and to learn more about our capabilities.