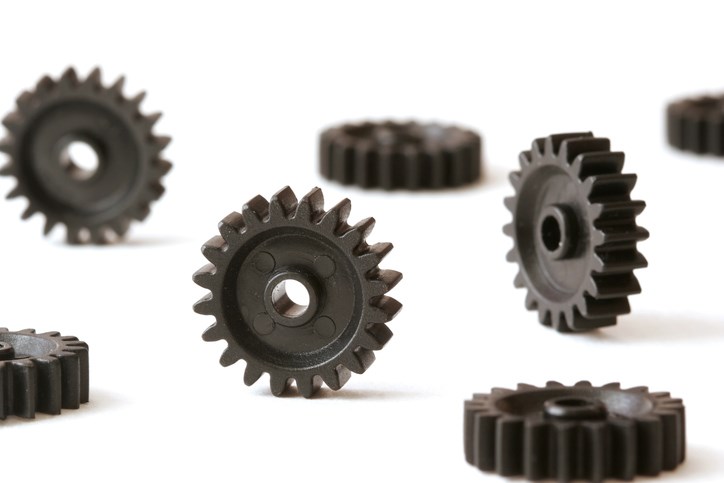
Thanks to their unique combination of properties, cost-effectiveness, and versatility,
plastic parts have become essential for nearly every industry. Naturally, this means that there are a wide range of demands placed on plastic components. While some applications call for simple components that perform a single function, others require parts that can withstand extremely demanding conditions (such as service temperatures exceeding 260°C) without losing functionality or performance. And, many times, industries require high-volumes of identical parts that all meet these high standards. To meet this demand, injection molding has become the go-to method for most. But why is injection molding good for mass production of plastic components? Let’s take a closer look.
Why is Injection Molding Good for Mass Production?
Injection molding is one of the most efficient plastic manufacturing processes out there. It involves injecting molten material into a pre-designed mold, which is then allowed to cool before it’s ejected as a fully formed component.
When it comes to answering the question, “why is injection molding good for mass production?” there are a number of key characteristics to consider:
High Efficiency and Speed
Injection molding is known for its rapid cycle times. Once the design is finalized and the tooling built, injection molding allows manufacturers to produce large quantities of parts in a relatively short period. The entire process can take as little as a few seconds to a couple of minutes per cycle, depending on the part's complexity and size.
The automated nature of the process, which has increased significantly in recent years, further minimizes the need for human intervention, which can speed up production. When your application calls for a regular supply of high-quality plastic components, no other manufacturing method compares to the capabilities of injection molding.
Consistency and Precision
Another one of the hallmarks of injection molding is its ability to produce highly consistent and precise parts with tight tolerances. The process relies on advanced machinery and molds that ensure minimal variation between parts. Why does this make injection molding good for mass production?
For one thing, it ensures that the same parts can be produced repeatedly and with uniformity across large production runs. This is especially important in industries like automotive and medical, where parts must meet stringent specifications. And second, the consistency of the parts produced means that manufacturers can rely on predictable performance and quality, reducing the risk of defects and the need for rework. This reliability not only enhances product performance but also builds customer trust and satisfaction, making injection molding a perfect choice for mass production.
Material Efficiency
Material efficiency is a significant advantage of injection molding, as the process allows for the precise control of material usage. This precision minimizes waste and ensures that the maximum amount of material is utilized during production. This is another big reason why injection molding is good for mass production.
By optimizing material use, manufacturers can lower production costs and reduce environmental impact. Efficient material usage also leads to less scrap and a more sustainable manufacturing process, making injection molding a financially viable option for high-volume production. This focus on material efficiency not only contributes to cost savings but also aligns with growing demands for sustainability in manufacturing.
Scale of Economies
And finally, the scale of economies achieved through injection molding is another reason why it is well-suited for mass production. As production volumes increase, the cost per unit decreases significantly.
When producing large quantities of parts, the initial investment in high-quality molds and machinery is spread across a greater number of units, resulting in lower costs per part. This scalability allows companies to remain competitive in their pricing while maintaining profit margins. As a result, injection molding not only meets the demands of mass production but also provides a cost-effective solution for businesses looking to grow in competitive markets.
How Does Injection Molding Compare with
Other Methods?
Naturally, injection molding is not the only manufacturing method available for the production of plastic parts. But when considering why injection molding is good for mass production, we would be remiss not to compare it with other solutions. Let’s take a look at a few:
Blow Molding — Blow molding is used primarily for creating hollow plastic parts by inflating a heated plastic tube inside a mold. While it’s good for producing large volumes of lightweight containers and bottles quickly, it’s less precise than injection molding and generally limited to simpler shapes. It excels in producing large, hollow parts but lacks the detail and tolerance levels of injection molded parts.
Thermoforming — Thermoforming involves heating a plastic sheet and forming it over a mold to create shallow parts. It’s a quick and cost-effective method for low to moderate production runs of large parts. However, like blow molding, thermoforming typically lacks the precision and material efficiency of injection molding and is better for simple shapes and larger components.
Rotomolding — Also known as rotational molding, this process uses a rotating mold to create hollow plastic parts by heating and cooling resin. It’s an excellent choice for creating large, hollow objects with uniform wall thickness. But, it’s generally slower than injection molding and not as precise, making it less suitable for high-volume production of intricate parts.
Compression Molding — Compression molding involves placing plastic material into a heated mold and applying pressure to form parts. It’s suitable for large, simple parts and can handle thick materials well. But while capable of producing large volumes, compression molding is less efficient than injection molding and does not offer the same level of precision or detail.
Extrusion — Extrusion involves forcing melted plastic through a die to create continuous shapes, such as pipes or sheets. It’s highly efficient for producing long, uniform shapes in high volumes, but it also lacks the ability to create the complex shapes and tight tolerances that injection molding provides. Extrusion is more suitable for simpler profiles.
3D Printing — 3D printing creates parts layer by layer using various additive manufacturing technologies. It’s highly versatile and is the only other method capable of producing complex geometries on demand. However, 3D printing is generally not suitable for high-volume production due to slower speeds and higher costs per unit. While it excels in prototyping and customization, it does not match the efficiency and cost-effectiveness of injection molding for mass production.
Thogus Specializes in High-Volume Injection Molding
At Thogus, we specialize in delivering high-quality injection molding solutions for diverse industries, including healthcare, consumer products, plumbing, automotive, and electronics. Our advanced capabilities include injection molding, engineering support, tooling, secondary operations, and metal-to-plastic conversions, allowing us to create complex parts with enhanced functionality and aesthetics.
With a commitment to excellence and a focus on innovation, we leverage state-of-the-art technology to meet the unique needs of each project. Partner with us for precision, efficiency, and superior results in your next high-volume injection molding project.
Experience the Thogus Difference
Connect with us today to discuss your project and to learn more about our capabilities.