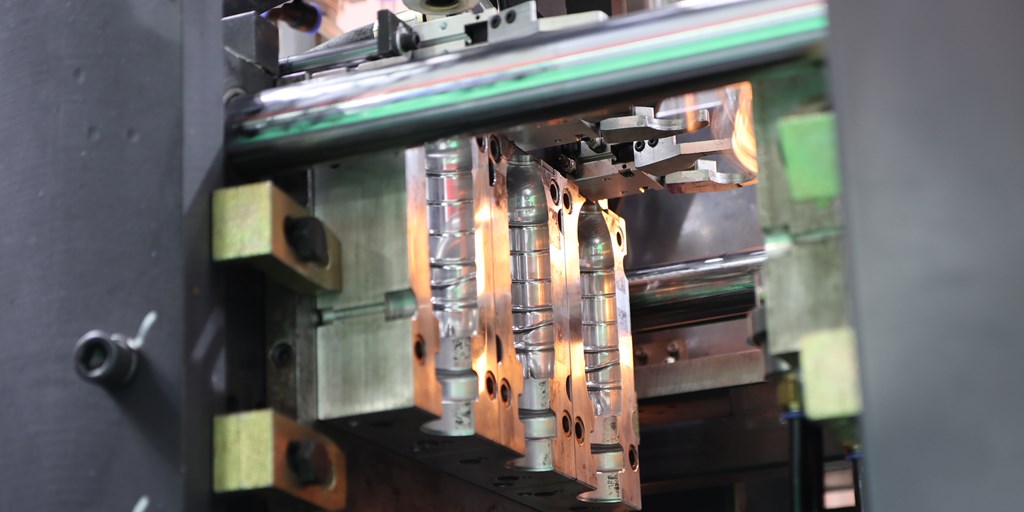
Without universally accepted guidelines, it can be difficult to figure out when your injection molding tooling needs replaced. The Plastics Industry Association (PLASTICS, formerly the Society of Plastics Industry or SPI) provides standards for mold classification that can help estimate tool life.
The five PLASTICS mold classifications are 101, 102, 103, 104 and 105, with Class 101 being the highest quality, cycles, and production levels, and 105 being the lowest quality, cycles, and production levels. Because wear and tear are side effects of mechanical processes, these estimates are based on injection molding shots (the number of times that mold is filled and opened), not on parts that are produced.
The following table represents estimated shot life by class.
Class |
Estimated Shot Life |
Class 105 Mold |
Not exceeding 500 |
Class 104 Mold |
500-100,000 |
Class 103 Mold |
100,000-500,000 |
Class 102 Mold |
500,000 to 1 million |
Class 101 Mold |
More than 1 million |
While these estimates are helpful in some circumstances, they don’t account for everything. After all, tooling doesn’t cap out after 1 million shots. Some of the tools here at Thogus run over a million shots annually; some have reached above 20 million shots before needing replacement.
The replacement schedule can be affected by a number of factors, from material selection to program requirements and preventative maintenance schedules, so it’s better to know how to identify specific issues in advance that might indicate tooling needs to be replaced, rather than relying on hard and fast rules based on shots or timelines.
You should start thinking about replacing tooling when any of the following issues are identified:
Increasing PPM Levels
One of the first signs that tooling needs to be replaced is that parts per million (PPM) trends start to increase. PPM numbers can be higher than expected for a variety of reasons, some of which are just a natural part of the tooling process. However, a sudden rise in PPM in a tooling process that has been smooth sailing is typically due to either tool conditions that cannot be improved or tool conditions that can be repaired temporarily, but then quickly fail.
Dropping On-Time Delivery Rates
Tooling that is breaking down causes delays due to greater needs for maintenance and rising PPM rates. When tooling reaches end-of-life, satisfying orders become a burden due to constant downtime. Possible causes of downtime could include waiting on lead times for tool repairs, increased scrap rates, or non-value post-production operations like trimming flash or part sorting.
Rising Costs
When tooling reaches end-of-life, program costs typically start creeping up. In addition to monetary costs, watch out for costs related to scrap rates, tool repairs, labor for sorting or other operations, and the chaos that comes from issues like orchestrating returns, line downs, and vendor management.
At-Risk Conditions
Your injection molder or toolmaker can identify at-risk conditions with your tooling, so you should be aware of them throughout the operation. Usually, at-risk conditions are maintained through repairs, but most repairs can only be made so many times before the tooling will need to be replaced. When repairs stop holding, or parts get worn down, it’s time to think about replacing your tooling.
The team at Thogus is made up of tooling experts who work with high-quantity projects and who know the ins and outs of tool maintenance. Success starts at the beginning: properly build tooling is one of the four pillars in our Manufacturing by Design process. Our expertise carries through to our in-house tooling maintenance, recommending improvements, and tooling and mold transfers. Learn more here.
Experience the Thogus Difference
Connect with us today to discuss your project and to learn more about our capabilities.