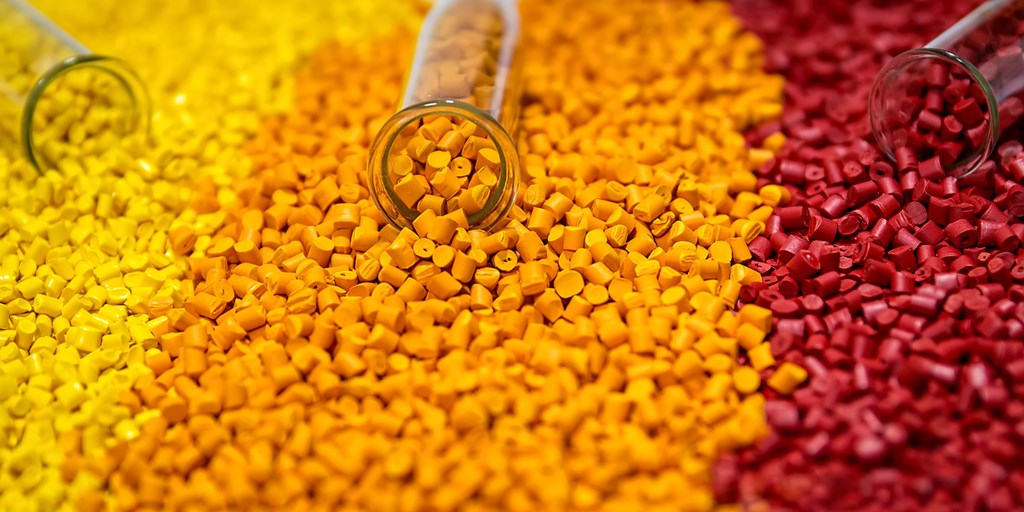
One well-known advantage of plastic injection molding over other manufacturing styles is the ability to add the coloring of the final product into the molding process, limiting the need for painting or plating after the fact. This characteristic of the plastic manufacturing process creates durable, long-lasting color that won’t wear off or smudge under harsh environmental conditions. However, because the addition of color is a chemical process in this scenario, manufacturers need to consider the available options to create the ideal combination of colorant and polymer material for each project.
Material selection is one of the most important considerations for a plastic injection molding project. The plastic resins you choose will help define many characteristics of your end product, including mechanical, thermal, and chemical properties. Depending on the end product goals, you may choose from a selection of commodity resins that are easy to work with, comparatively inexpensive, and ideal for environments that don’t impose significant performance demands, or you may choose from a selection of custom resins which, while more expensive, can be engineered to meet the demands of harsh conditions. When considering adding colorant to a polymer, it’s important to be aware of the physical and chemical properties of the polymer you have chosen, as it can affect the coloring process.
Color can be incorporated into a resin in several ways. Masterbatch offers a concentrated mixture of pigments or additives combined with a carrier resin and transported in liquid or pellet form. Masterbatch is usually the preferred method for coloring plastic polymers as it is easy to work with, offers excellent color distribution, and can be easily adjusted. Alternatively, pure pigments in the form of colored pellets or compounds can also be used. Finally, powdered colorants are an inexpensive option.
Taking the Heat
The plastic injection molding process relies on very high temperatures to liquidate the plastic polymers or, in some cases, to set the plastic in the mold. These high temperatures make the addition of colorant a particularly delicate process. Some combinations of colorants and polymers are simply not compatible; the colorant must be able to survive the temperature of the manufacturing process, which varies from polymer to polymer. If the polymer must be processed at a higher temperature than the colorant can withstand, that pairing won’t be an option.
Chemical Reactions
High manufacturing temperatures also cause chemical reactions to occur more rapidly, and the addition of colorant can affect the properties of plastic polymers. For example, it’s possible for the compounds in a particular colorant to break down the chemical composition of certain polymers. If that’s the case, then a polymer that was chosen because of its durability can lose that property when the colorant is added.
The degree of effect the colorant has can be determined by a number of factors. Just as molecular weight (the sum of the weight of all the atoms in the molecule) can determine properties of a polymer, like making it heavy enough to block radiation, it is also a property of colorants that affects how they interact with plastic polymers. Crystallinity, or the structure of the molecules, is another contributing factor.
Logically, the more colorant that is added the more pronounced these effects can be. Generally, manufacturers try to keep the colorant concentration between 1% and 4% based on colorant end product requirements. Some polymers are naturally translucent, others are opaque, and all have varying natural hues. The difference between the natural color of the polymer and the desired color of the end product can determine what concentration of colorant is necessary.
Using Color
The color of plastic materials is not just cosmetic, it plays into the function of the part. Adding color to containers can help protect the contents from harmful UV rays, or can improve the weather resistance of a plastic part. Coloring can also be used as a simple form of communication to indicate type or function. However color is used, it must be incorporated in the design of the product in a way that doesn’t compromise its overall purpose.
Concerned about finding the right combination of polymer and colorant? Rely on the material expertise at Thogus for your manufacturing needs.
Experience the Thogus Difference
Connect with us today to discuss your project and to learn more about our capabilities.