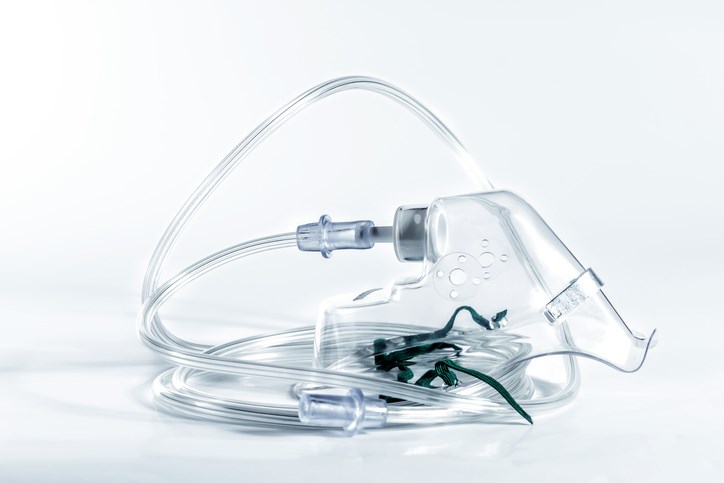
Once an industry dominated by glass, metal, and rubber, the medical device industry has increasingly turned to high-quality plastics in recent years. In fact, plastic components have become vital for everything from disposables and single-use medical products to highly technical implantable devices and diagnostic equipment. As a result, extremely high standards are placed on plastics used in medical devices to the point that a sub-category, medical-grade plastic, has developed. But what is medical grade plastic and what differentiates these materials from other polymers? Let’s explore some of the most common medical grade plastics, the characteristics that make them suitable for medical applications, and the manufacturing considerations involved during production.
What is Medical-Grade Plastic: Properties
Medical-grade plastics usually stand out from other injection molding polymers in a few key ways. One of the most essential is biocompatibility. Biocompatibility ensures that materials can safely interact with biological systems without causing adverse reactions. This is particularly important for components that come into direct contact with bodily fluids and tissues, such as implants, catheters, and syringes.
Sterilizability is another key property, as the ability to sterilize medical plastics is essential for ensuring that medical devices are free from contaminants and safe for patient use. And finally, medical-grade plastics usually exhibit superior physical properties (including transparency for certain applications like lenses and IV solutions) and chemical resistance to ensure parts can withstand exposure to various sterilizing agents, disinfectants, and biological substances.
Common Medical-Grade Plastics Used in Injection Molding
With some of the most basic properties in mind, what is medical grade plastic specifically? There are a large number of polymers that can qualify, but a few of the most widely used are:
- Polyethylene (PE) — Polyethylene is a widely used polymer known for its excellent chemical resistance and durability. As a medical-grade plastic, it is often utilized in applications such as packaging, medical tubing, and disposable devices. Its biocompatibility ensures that it can be safely used in contact with bodily fluids. Low-density polyethylene (LDPE) and high-density polyethylene (HDPE) variants are particularly valued for their flexibility and strength, making them suitable for a variety of medical applications.
- Polypropylene (PP) — Polypropylene is a versatile polymer recognized for its high resistance to heat, chemicals, and moisture. In the medical field, it’s frequently used in the production of syringes, containers, and surgical instruments. Polypropylene is also biocompatible and can be sterilized using various methods, including autoclaving. Its lightweight nature and rigidity make it an ideal choice for medical devices requiring both strength and ease of use.
- Polycarbonate (PC) — Polycarbonate is a strong and transparent thermoplastic known for its impact resistance and optical clarity. Its medical-grade formulations are used in applications such as medical devices, protective eyewear, and surgical equipment. The biocompatibility of polycarbonate makes it suitable for direct contact with the human body. Additionally, its ability to withstand sterilization processes adds to its appeal in medical settings, ensuring safe and reliable performance.
- Polyetheretherketone (PEEK) — Polyetheretherketone (PEEK) is a high-performance engineering thermoplastic renowned for its exceptional strength, thermal stability, and chemical resistance. As a medical-grade plastic, PEEK is commonly used in implants, surgical instruments, and dental applications due to its biocompatibility and ability to withstand harsh sterilization processes. Its excellent mechanical properties and dimensional stability also make it suitable for high-load applications in medical devices, where reliability and performance are critical.
Manufacturing with Medical-Grade Plastics: Why Injection Molding is the Gold Standard
Now that we’ve answered the question, “what is medical-grade plastic?”, the next thing to consider is why injection molding is often the go-to manufacturing method for working with these materials. Injection molding exhibits several key characteristics that address the unique demands of the medical industry. A few of these include:
High Precision and Consistency
One of the primary advantages of injection molding in medical manufacturing is its ability to produce parts with exceptional precision and consistency. The process utilizes advanced machinery and molds designed to maintain tight tolerances, ensuring that each component meets stringent specifications required in medical applications. This level of accuracy is crucial for devices that must perform reliably in critical situations, such as surgical instruments and implantable devices.
Scalability
Injection molding is inherently scalable, making it ideal for both small and large production runs. Once the mold is created, manufacturers can produce thousands or even millions of identical parts with minimal variations. This scalability allows medical device companies to meet varying demand levels without compromising quality, which is vital in an industry where supply chains can be unpredictable.
Design Flexibility
The injection molding process supports a wide range of design possibilities, enabling manufacturers to create complex geometries and intricate features. This design flexibility is particularly beneficial in the medical field, where innovation often drives the development of new devices. Manufacturers can also integrate multiple functionalities into a single part, reducing assembly time and enhancing the overall performance of the final product.
Cost-Effectiveness
While the initial investment in molds can be substantial, injection molding offers long-term cost savings through reduced labor and material costs. The ability to produce high volumes of parts with minimal waste ensures that the overall cost per unit decreases significantly with larger production runs. On top of that, the durability of medical-grade plastics used in injection molding often leads to lower maintenance and replacement costs for medical devices.
Shorter Lead Times
The efficiency of the injection molding process contributes to shorter lead times for medical device production. With the ability to quickly manufacture and deliver large quantities of parts, manufacturers can respond rapidly to market demands and regulatory requirements. This speed is particularly crucial in the medical industry, where timely availability of components can impact patient care and safety.
Material Efficiency
Injection molding is a material-efficient process that minimizes waste during production. By precisely controlling the injection of molten plastic into molds, manufacturers can maximize the use of raw materials and reduce scrap. This efficiency not only lowers production costs but also aligns with the growing emphasis on sustainability in manufacturing, making it an attractive option for companies looking to reduce their environmental footprint.
Manufacturing Considerations When Working With Medical-Grade Plastics
When working with medical-grade plastics, it is essential to choose the right materials. Knowing which ones meet stringent industry standards for biocompatibility, chemical resistance, and mechanical strength is the foundation for successful medical device manufacturing. The right material will ensure that components perform safely in their intended applications. Alongside material choice, tooling and mold design are critical, as precision is vital for achieving consistent quality and minimizing defects.
Effective process control and optimization further enhance the manufacturing of medical-grade plastics. These factors require meticulous monitoring of parameters like temperature and pressure to ensure compliance with quality standards.
Trust Thogus With Your Medical Plastic Components
At Thogus, we’ve been a trusted supplier of injection molded plastic components for the medical industry for decades. We specialize in high-volume production runs for a wide range of critical applications. We also offer end-to-end solutions, including manufacturing by design support, material selection, post-production processes, and cleanroom assembly. Whatever your needs, we’re here to deliver tailored solutions for your applications.
Contact our team today to get started.
Experience the Thogus Difference
Connect with us today to discuss your project and to learn more about our capabilities.