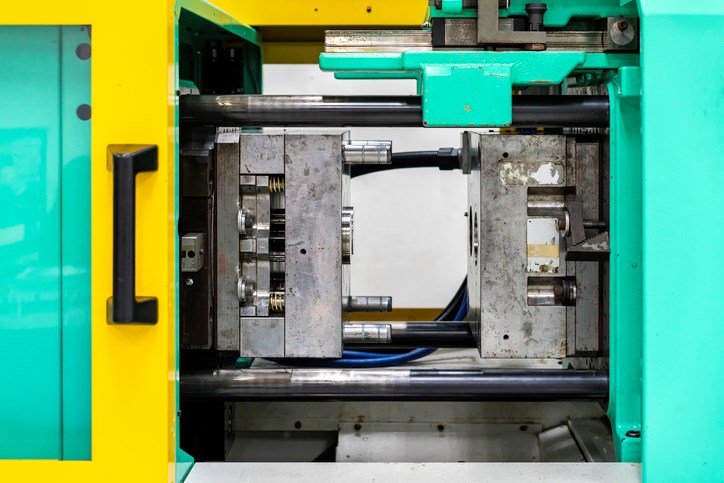
While injection molding is one of the most widely used manufacturing processes for producing plastic components, it still comes with a long list of challenges. The complexities involve factors such as material selection, mold design, tooling, and quality control. All of which require a high degree of expertise and manufacturing proficiency. One of the biggest challenges that manufacturers face is in the process itself. Inadequate material distribution, for instance, can lead to air pockets, surface finish issues, and other part defects that can negatively affect performance and functionality. That’s where manufacturers can benefit from the advantages of gas-assisted injection molding.
Gas-assisted injection molding is a variation of traditional injection molding. The distinction is in the use of nitrogen gas to assist in the molding process. Suitable for producing very complex parts, the advantage of gas-assisted injection molding lies mostly in its versatility and efficiency.
How Gas-Assisted Injection Molding Works
Gas-assisted injection molding works by using nitrogen gas to create hollow sections or thicker ribs in a plastic part. It’s a multi-step process that enhances design flexibility, material efficiency, and overall quality of molded parts.
The process begins with a small amount of molten material being injected into the mold. This initial shot creates a solid outer skin, which is usually smaller than the desired thickness for the finished part. Once that is in place, high-pressure nitrogen gas is released through a valve. This gas flows into the thicker sections or hollow areas and displaces the molten material outward toward the cavity walls.
While maintaining this gas pressure, molten material continues to flow and pack around the gas core. Ultimately, this helps ensure even distribution of plastic material along cavity walls and ensures the formation of voids.
The Biggest Advantages of Gas-Assisted Injection Molding
Reduced Material Usage
Because gas-assisted injection molding displaces plastic material in the interior of the part, lightweight parts can be produced without compromising structural integrity. This process also reduces the need for excess material by eliminating thick walls and solid sections that would need to be trimmed away in traditional injection molding processes.
Improved Part Quality
Another advantage of gas-assisted injection molding is the control it gives manufacturers over the filling of the mold. Because of this, defects like sink marks, unwanted voids, and warping can be minimized. The even distribution of material also contributes to reduced stress and fewer aesthetic defects on the surface, as well as enhanced dimensional accuracy.
Complex Geometries and Lightweight Parts
Possibly the most significant advantage of gas-assisted injection molding lies in its ability to produce parts with complex geometries and varying wall thicknesses. The gas core can be strategically placed to create thicker ribs or hollow sections, which makes it possible to design intricate and more innovative components. This is particularly valuable in industries like the automotive industry and consumer goods, where large and lightweight parts with intricate structures are in high demand.
Shorter Cycle Times
Shorter cycle times are another possible advantage of gas-assisted injection molding. Because the gas core in the mold acts as a heat insulator, the thicker portions of the component can cool more efficiently. This can significantly reduce the amount of time that each part spends in the mold, allowing for increased production efficiency and a reduction in manufacturing costs overall.
Decreases Wear and Tear on Tooling and Equipment
While gas-assisted injection molding does require specialized tooling and equipment, it’s also known for causing less wear and tear than traditional processes. With the gas acting as a guide for the molten material, the pressure for the material injection can be reduced, which puts less pressure on the mold. By reducing the need for frequent mold replacement and/or maintenance, this can also lead to cost savings in the long run.
Design Flexibility and Innovation
Finally, one of the other major advantages of gas-assisted injection molding lies in the possibilities for design flexibility and innovation. Due to the versatility of the process, designers have more freedom to create parts with unique shapes, structural features, and improved functionality. This, in turn, opens the door for even more customization and novel solutions for meeting challenges in a variety of industries.
Which Industries Should Consider Gas-Assisted Injection Molding?
While nearly every industry can benefit from the advantages of gas-assisted injection molding, it’s a particularly invaluable process in the following areas:
- Automotive — In the automotive industry, reducing the weight of components is essential to improving fuel efficiency. Gas-assisted injection molding allows for the creation of lightweight but structurally sound parts, which can lead to significant weight savings in components like interior trim, door panels, and other structural elements.
- Consumer Goods — Many consumer goods like household appliances, furniture, and electronics require high-quality surface finishes. Gas-assisted injection molding helps produce parts with reduced aesthetic defects and better ergonomic designs.
- Medical Devices — Medical devices often require personalized or patient-specific components. Gas-assisted molding allows for the efficient production of precise, intricate components that ensure better fit and functionality.
- Industrial Applications — In industrial applications, parts often need to withstand heavy loads and extreme conditions. Gas-assisted molding can create parts with thicker ribs, enhanced strength, and improved structural stability.
Experience the Advantages of Gas-Assisted Injection Molding with Thogus
At Thogus, we’re proud to deliver fully custom injection molding services for a wide range of industries. Our capabilities include insert molding, overmolding, two-shot, and gas-assisted injection molding. With a team of dedicated experts and the latest in advanced manufacturing equipment and automation systems, we specialize in mid- to high-volume manufacturing of critical plastic components.
Our commitment to quality doesn’t just cover our manufacturing services; we’re also passionate about delivering the best in white glove customer service so you can be sure that you’ll have a fully collaborative partner from start to finish.
Whether you’re looking for gas-assisted injection molding, traditional injection molding, engineering support, or secondary operations, we have the expertise and capabilities to deliver.
Reach out today to get started.
Experience the Thogus Difference
Connect with us today to discuss your project and to learn more about our capabilities.