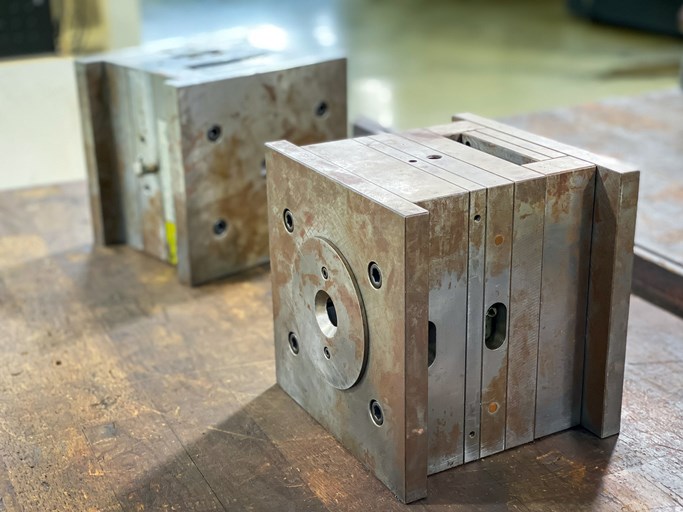
Injection molding is a manufacturing process known for its precision, efficiency, and unmatched consistency in quality. This is largely thanks to plastic injection molding tooling, which is what allows manufacturers to achieve high-performance parts that meet the demands of critical industries. In fact, selecting the right tooling is critical for project success. But what exactly does that selection process entail?
First, it’s essential to understand tooling classes. These classifications define mold durability, intended lifespan, and production volume capacity. Whether you’re producing a prototype or a high-volume production run, choosing the correct tooling class ensures a cost-effective and reliable manufacturing process. Let’s break down the different tooling classes, their applications, and how to determine the right option for your next project.
What Are Injection Molding Tooling Classes?
Derived by the Society of Plastic Industry (SPI), plastic injection molding tooling classes are standardized categories that help manufacturers determine the best mold type based on production needs. These classifications are based on factors like durability, expected production volume, and cost considerations. The five primary classes run from Class 101 to Class 105.
A Breakdown of Tooling Classes and Their Applications
Class 101: Extremely High-Volume Production
Cycles: 1,000,000+
Class 101, the most durable of the plastic injection molding tooling classifications, encompasses tools that are designed to handle extremely high production volumes — typically over a million cycles. These molds are often made from hardened steel and feature advanced cooling and wear-resistant components to ensure long-term performance. While they require a higher upfront investment, their durability makes them cost-effective for large-scale manufacturing.
Class 101 tooling is ideal for industries that require continuous, high-precision production, like automotive, electronics, and medical devices. Products like automotive interior components, high-volume electronic housings, and medical-grade plastic parts often rely on Class 101 molds for consistent quality and efficiency.
Class 102: Medium-High Volume Production
Max Cycles: 1,000,000
The next category of plastic injection molding tooling is Class 102. Built for moderate to high-production volumes, these molds are typically made from hardened steel, though they may have fewer premium features than Class 101. They are a cost-effective solution for projects that don’t require extreme longevity.
Class 102 tooling is commonly used in consumer products, industrial components, and medical applications where production volumes are substantial but don’t justify the investment in Class 101 molds. Items like appliance components, durable packaging, and mid-to-high volume medical parts often utilize this tooling class.
Class 103: Medium Production
Max Cycles: 500,000
The third category of plastic injection molding tooling is Class 103. Class 103 molds are designed for moderate production runs, typically supporting up to 500,000 cycles. Often made from a mix of hardened and pre-hardened steel, they lack the extended lifespan of Class 101 and Class 102 molds; however, they’re ideal for projects that require consistent quality without the need for extremely high volume output.
Class 103 tooling is a popular choice for consumer goods, industrial components, and low- to mid-volume automotive parts. It’s an excellent choice for manufacturers who need reliable performance but want to manage tooling investment costs efficiently.
Class 104: Low Production
Max Cycles: 100,000
Class 104 molds are a category of plastic injection molding tooling that is more suited for short-run production. Made from softer materials like aluminum and mild steel, these molds have much lower upfront costs and a shorter lifespan than the high-class tooling options. As a result, they provide an efficient and cost-effective solution for low-volume projects.
Class 104 tooling is great for prototype development, market testing, or specialty product runs. Manufacturers looking to refine a design before committing to full-scale production often use this class to validate part performance while keeping costs down.
Class 105: Prototype Tooling
Max Cycles: 500
The final category of plastic injection molding tooling is Class 105. Made from low-cost materials like aluminum and soft steel, these molds are extremely fast to produce and modify. The primary function of this class is to validate part designs before investing in high-grade production tooling.Class 105 tooling is ideal for early-stage product development, concept testing, and design verification. This class allows manufacturers to quickly iterate on designs, test functionality, and refine components before committing to full-scale production — saving both time and costs in the long run.
How to Select the Right Tooling Class for Your Project
Choosing the right plastic injection molding tooling class is essential for balancing cost, durability, and production efficiency. The best option depends on several key factors:
- Production Volume: High-volume runs require durable tooling (Class 101 or 102), while low-volume or prototype projects can use softer materials (Class 104 or 105).
- Material Selection: The type of plastic being molded affects tooling wear. Abrasive or high-temperature resins may require harder, more durable tooling.
- Budget Constraints: Higher-class molds have greater upfront costs but lower per-part costs in large production runs. Lower-class molds offer affordable entry points for short-term or prototype needs.
- Product Lifecycle: If a product is expected to undergo design changes, lower-class tooling (Class 104 or 105) allows for quick modifications. For stable, long-term production, investing in high-grade tooling is more cost-effective.
Understanding these factors helps manufacturers select the most efficient and cost-effective tooling class for their specific application needs — ensuring both performance and long-term value.
Experience Thogus’s Expertise in Tooling and Design
At Thogus, we bring decades of expertise in injection molding tooling and design, ensuring that every project is optimized for efficiency, quality, and cost-effectiveness. Our team works closely with clients to assess production needs, recommend the ideal tooling class, and deliver precision-engineered molds that align with their manufacturing goals.
Whether you need high-volume production molds or cost-effective prototype tooling, we have the experience, advanced technology, and commitment to quality to bring your project to life. Let us help you select the right tooling class to maximize performance and long-term value.
Ready to get started? Contact Thogus today to discuss your injection molding needs.
Experience the Thogus Difference
Connect with us today to discuss your project and to learn more about our capabilities.