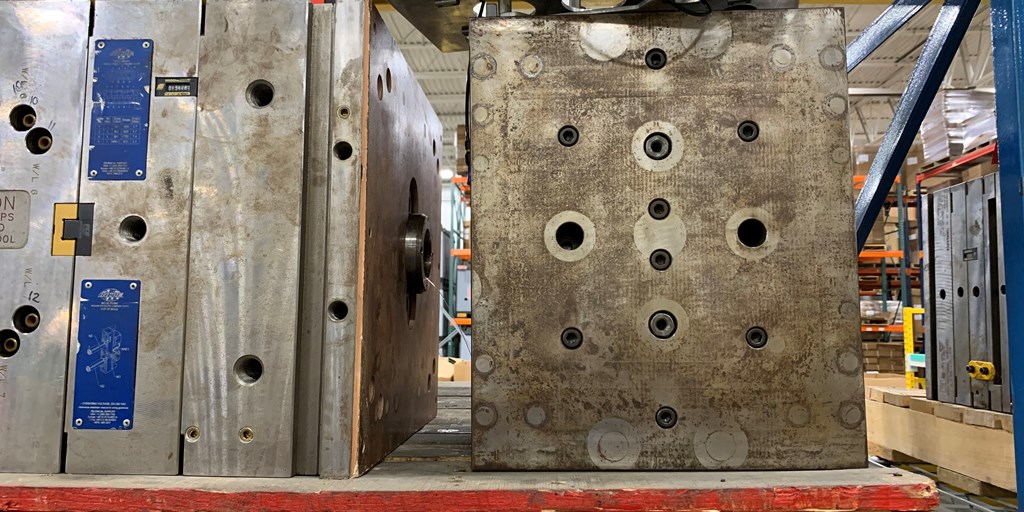
Your plastic injection molding tooling affects every aspect of your manufactured product. Creating your tooling is also one of the most expensive parts of the injection molding manufacturing process, so the last thing you need to worry about is premature wear and tear.
That’s why in order to have a long-lasting tool, it’s important to pay close attention to proper maintenance by implementing a regular upkeep schedule.
Tool Design Dictates the Maintenance Plan
Maintenance really begins with the design of the tool. Generally speaking, tooling is classified on a scale from 101 to 105. Class 101 is the most durable, often made of hard steel and guaranteed for 1 million or more shots.
Class 105, conversely, is likely to be an aluminum prototype. Performing a risk assessment upfront as you begin designing a tool allows you to identify critical areas that have a higher risk of damage, difficulty cleaning, and risk of failure. You can then make sure that when the tool is created those areas are inserts, allowing them to be repaired or replaced easily. The best way to make sure that your tooling lives up to its maximum number of shots is to develop a preventative maintenance program to give your tooling the care it needs before any problems arise.
Think of the preventative maintenance plan for your tooling the way you think of maintenance on your car: everything has to be done according to a schedule, which is based on factors like time in use, number of runs, and wear and tear. Your plan should be based on the unique needs of your tool, so you’ll need to assess those first. Once those problem areas are accounted for, the rest of your preventative maintenance plan should focus on a schedule for cleaning and maintaining the tool to ensure maximum uptime.
Proper Use is Key
It’s also important to make sure that you are running the tool appropriately, with the right tonnage and setup to ensure the best possible performance. Incorrect application of pressure or use of materials will cause already fragile components to break down much more quickly, necessitating replacements and a more rigorous cleaning and repair schedule.
Limit the core pressure and speed to what is necessary for the application, making sure not to burn out the tooling before its time. Likewise, the mold temperature should be kept to just the level that is needed for the part — high mold temperatures can adversely affect the tooling life.
Preventative maintenance plans should come part and parcel with your tool design and manufacture. Your injection molding manufacturing partner should design the plan for you based on the unique characteristics and needs of your machine.
At Thogus, we’ve been working with tooling since 1950. We have our own proprietary line of tube and hose fittings, and our tools have seen tens of millions of shots, so we know what it takes to build durable tools and robust preventative maintenance plans.
Contact us today to get started!
Experience the Thogus Difference
Connect with us today to discuss your project and to learn more about our capabilities.