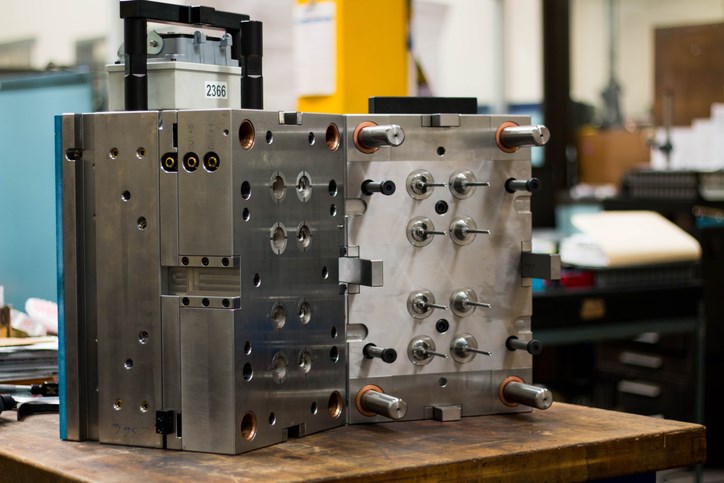
In injection molding, tooling is the key to successful production, whether you need simple parts or highly complex custom components. The precision and efficiency of the molds used are a major determinant of overall part quality, consistency, and cost-effectiveness. This is especially true when producing custom plastic products, where specialized tooling is often required in order to achieve the desired features, tolerances, and finishes.
Without the right tooling strategy in place, even the most advanced injection molding processes can fall short. Properly managed tooling ensures that the parts meet design specifications and that they can be produced in high volumes, efficiently and without defects. Let’s take a closer look at why that is.
For a look at the role of tooling in complex molding projects, check out Part 1: Complex Molding and the Challenges of Manufacturing Precision Parts.
What is Tooling Management in Injection Molding?
Tooling management in injection molding happens throughout the lifecycle of the mold — from initial design and manufacturing to ongoing maintenance and optimization. Each step is crucial when it comes to ensuring the quality, consistency, and efficiency of the production process, especially for custom plastic products where precision and performance are paramount.
In general, tooling management involves:
- Design — The tooling design phase is where the foundation for a successful injection molding process is established. Every detail — including material flow, cooling channels, and part ejection — must be carefully engineered to meet specific part requirements.
- Manufacturing — Once the design is finalized, the next step is the manufacturing of the mold. This often involves using high-grade materials and advanced manufacturing techniques, like CNC machining or 3D printing, to create a mold that matches the project parameters. The precision of this step informs the overall quality of the parts that will be produced.
- Maintenance — Tooling maintenance is sometimes an overlooked aspect of injection molding, but it's critical for ensuring long-term success. Regular inspections, cleaning, and repairs prevent wear and tear from impacting the mold’s performance. Poorly maintained molds can lead to inconsistent part quality, increased downtime, and unexpected costs due to defects or production stoppages.
- Optimization — Over time, even the best-designed molds can benefit from adjustments and optimization. Whether it’s fine-tuning cooling channels to reduce cycle times or modifying parting lines to improve part aesthetics, optimization is key to staying competitive, increasing efficiency, reducing material waste, and ultimately lowering production costs.
Achieving Effective Tooling Management in the Manufacturing of Custom Plastic Products
Early Involvement in Tool Design
Involving the manufacturer early in the tooling design process is a critical part of achieving effective tooling management in the manufacturing of custom plastic products. By bringing in manufacturing expertise at this stage, businesses can ensure that the tool is not only capable of producing the desired parts. Manufacturers can also provide valuable insights that help align the tooling and product design with the realities of the production process.
This early collaboration helps ensure that the mold will be designed for manufacturability, which can minimize the risk of defects, downtime, or costly rework later on. For maximum effect, look for a manufacturer who offers engineering support. Engineering teams are invaluable for increasing the longevity of tooling and eliminating potential problems before they arise in full-scale production.
Tooling for Complex Custom Parts
For the production of complex custom plastic products, you’ll need molds that can accommodate capabilities like multiple materials, overmolding, or components with extremely tight tolerances. For instance, in 2-shot injection molding, where two different materials are molded within the same cycle, the tooling needs to be carefully designed to manage the sequential injection of materials without causing defects.
Gas-assisted injection molding is another capability that requires specialized tooling design. Gas-assisted molding involves injecting gas into the mold cavity to create hollow sections, which can reduce material use and cycle time — but only if the tool is designed with precise control over gas flow and venting.
Optimizing Tool Design for Efficiency
Efficiency is one of the most important aspects of manufacturing for almost every industry. Fortunately, there are a few ways that manufacturers can achieve this through effective tooling management. Working with manufacturers that offer engineering support means that you can focus on creating molds that produce high-quality parts and operate efficiently to reduce cycle times and minimize material waste.
And while investing in high-quality tooling often requires higher upfront costs, the long-term savings and operational benefits far outweigh that initial investment. Along with being more efficient, well-optimized tools also last longer and require less maintenance. This translates into fewer production disruptions and lower repair and replacement costs over time.
Maximizing Return on Investment (ROI)
The best approach to tooling management for custom plastic products doesn’t just aim to create high-quality molds — it also balances initial costs with long-term gains. When manufacturers invest in well-designed tooling, the benefits over time can far outweigh the the upfront expense by:
- Reducing defects like sink-marks, warping, or flashing
- Facilitating faster cycle times so more parts can be produced in less time
- Decreasing the need for repairs with tooling that is designed for longevity
- Reducing unexpected downtime by ensuring production lines stay operational
Ongoing Tool Maintenance
Routine maintenance is a crucial part of effective tooling management for custom plastic products. Even the best-designed tools require some regular care for continued performance. Routine maintenance like cleaning, polishing, and inspecting for wear or damage helps extend the life of these tools without losing out on performance.
One of the biggest risks of neglecting tool maintenance is unexpected downtime. A tool failure during production can stop operations, delay deliveries, and increase overall costs. But by proactively addressing potential issues before they escalate, manufacturers can prevent the need for expensive repairs or replacements, saving both time and money in the long run.
Collaborate with the Experts at Thogus For Your Custom Plastic Products
At Thogus, we pride ourselves on delivering high-volume, high-precision injection molding solutions that are customized to meet your specific requirements. With our extensive expertise in tooling management, we ensure that every project runs smoothly — from design and production to ongoing tool maintenance and repair. Our advanced technology and commitment to quality enable us to handle even the most complex custom parts efficiently and cost-effectively.
Whether you need support with custom resins, intricate tool designs, or secondary operations, our team of experts is ready to provide the engineering support and white glove service that set us apart in the industry.
Reach out to us today to learn how we can help you achieve the best possible results for your next project.
Experience the Thogus Difference
Connect with us today to discuss your project and to learn more about our capabilities.