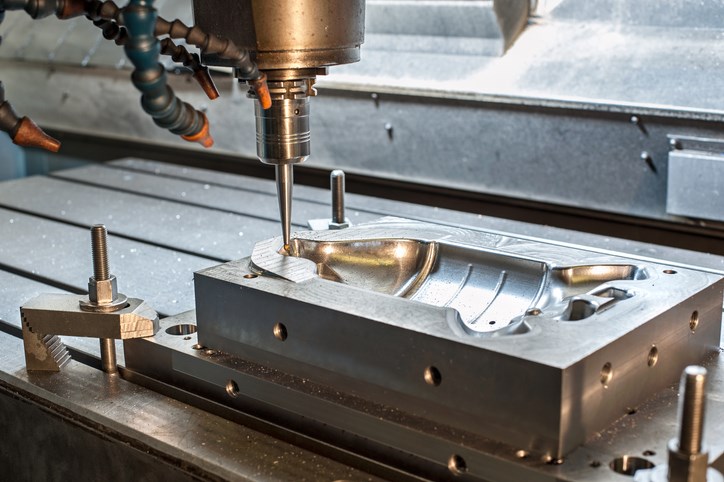
Precision is one of the first words that comes to mind when most people think of injection molding. That’s why it’s the manufacturing method of choice when strict tolerances are essential. For applications in industries like automotive and medical devices, tolerances help ensure that parts fit seamlessly into assemblies for long-term reliability and function.
At the heart of these capabilities are tooling and design. The right tooling setup and thoughtful design choices lay the foundation for accuracy, consistency, and efficiency. Let’s explore how these factors come together to maintain exacting tolerance standards.
Understanding Injection Molding Tolerance Standards
In injection molding, tolerances refer to the allowable variation in a part’s dimensions, ensuring that each part aligns with the intended specifications. These precise standards are vital for maintaining consistent fit, function and performance; tight tolerances can even help minimize assembly issues and uphold the overall quality of the final product.
Several industries call for unwavering precision in injection molded components. A few of these include automotive (sensors and connectors), medical devices (surgical instruments and diagnostic equipment) and electronics (housings and connectors).
The Impact of Tooling on Injection Molding Tolerance Standards
When it comes to maintaining strict tolerance standards, high-quality tooling is non-negotiable. The better the tooling, the fewer deviations in the final product, reducing the need for rework or adjustments. But tooling isn’t just a one-time investment — it’s a critical asset that requires ongoing maintenance to prevent wear and tear that can compromise tolerance standards. Proactive inspections, cleaning, and repairs help ensure that tools remain in peak condition.
At Thogus, we utilize state-of-the-art tooling techniques and materials to craft molds that meet the highest standards of accuracy and durability. Plus, our comprehensive maintenance services are designed to extend tool life while ensuring consistent precision over time.
How Design Choices Influence Tolerance Standards
To achieve tight tolerances, everything starts with thoughtful design. Early-stage decisions during the design process can significantly influence whether or not precision standards are met. By integrating Design for Manufacturability (DFM) principles, designers can ensure that parts are optimized for efficient and accurate injection molding.
Some design elements have a greater impact on tolerances than others. For instance:
- Part Geometry: Complex shapes or intricate details can increase the likelihood of deviations. Simplifying designs where possible can improve precision.
- Wall Thickness: Inconsistent wall thickness can lead to uneven cooling, resulting in warping or shrinkage. Maintaining uniform thickness is critical for accuracy.
- Material Selection: The properties of the chosen polymer—such as its shrinkage rate and resistance to deformation—play a significant role in achieving precise dimensions.
At Thogus, we prioritize collaboration between our engineering team and clients during the design phase. This partnership ensures that every aspect of the part — down to the smallest detail — is tailored to achieve manufacturability without sacrificing quality or function.
Implementing Advanced Technologies for Tolerance Management
And finally, achieving precise tolerances begins well before production. At Thogus, we utilize cutting-edge molding simulation software to predict and optimize part performance during the design phase. This advanced technology allows our engineering team to analyze key factors — such as material flow, cooling rates, and potential shrinkage — to ensure that tolerances are met from the outset.
Once production begins, maintaining consistent quality requires careful oversight. By employing real-time monitoring systems and automation, manufacturers keep processes on track and ensure every part meets exact specifications.
At Thogus, our commitment to state-of-the-art manufacturing technology not only enhances precision but also drives efficiency, helping us deliver exceptional quality while meeting tight deadlines.
Ready to Experience Quality and Accuracy? Turn to Thogus
At Thogus, precision is at the foundation of everything we do. With decades of expertise and a commitment to cutting-edge technologies, we deliver injection molded components that meet the most demanding tolerance standards. From advanced tooling techniques to collaborative design services and real-time production monitoring, our team ensures every part exceeds expectations in quality and performance.
Whether you’re in the automotive, medical, electronics, or any other high-precision industry, Thogus has the capabilities to support your project from start to finish. Our proven track record in tooling innovation, design optimization, and scalable production solutions makes us the trusted partner for clients nationwide.
Contact us today to discuss your custom injection molding needs and discover why we’re a leader in precision manufacturing.
Experience the Thogus Difference
Connect with us today to discuss your project and to learn more about our capabilities.