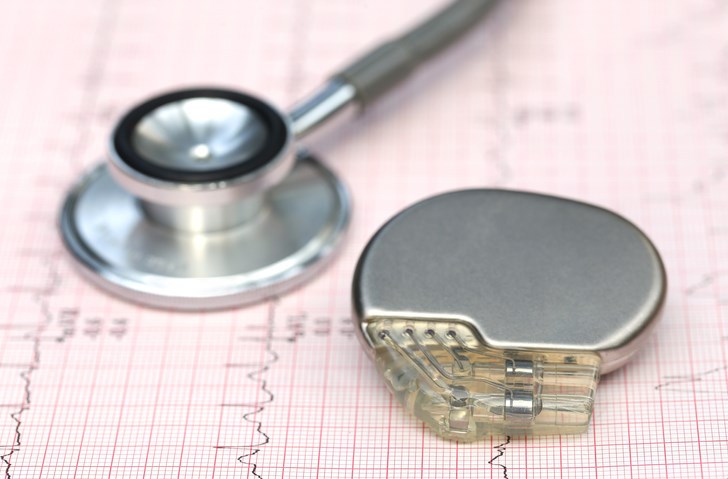
In medical device plastic part manufacturing, selecting the right material is paramount. Not only is it an important step toward ensuring product safety, efficacy, and performance, but the right resin can also facilitate a smoother production process. Fortunately, there are a variety of options available when it comes to choosing the right materials for medical device plastic components. With that in mind, let’s take a closer look at the role of plastic components in medical devices and explore some of the most common plastics used in medical devices.
The Role of Plastics Used in Medical Devices
Plastics used in medical devices are also classified as medical grade plastics. These materials meet the stringent regulatory and quality standards for use in medical devices and equipment. Specifically, medical grade plastics exhibit properties that help ensure safety, biocompatibility, and the continued integrity of the medical device. A few of these properties include:
- Sterilization compatibility—Plastics used in medical devices need to be able to withstand various sterilization methods such as steam autoclaving, ethylene oxide sterilization, and gamma radiation.
- Chemical Resistance—Medical grade plastics are often exposed to a lot of chemicals. Because of that, high chemical resistance is necessary so that the material properties stay stable over a long period of time.
- Durability and mechanical properties—Strength, flexibility, and impact resistance are important for a variety of medical device applications. This particularly applies to medical devices that must endure repeated use.
- Radiopacity and imaging compatibility—Some medical devices, such as those used in diagnostic imaging or minimally invasive procedures, need plastics with radiopaque properties. This enables these devices to be visible under X-ray or other imaging technology.
The Most Common Plastics Used in Medical Devices
Polyethylene (PE)
Polyethylene is a plastic used in medical devices due to its excellent chemical resistance, flexibility, and biocompatibility. It is also lightweight and stands up well to moisture solvents, which makes it ideal for disposable syringes and various orthopedic implants and prosthetic components.
Polypropylene (PP)
Polypropylene shares a lot of the same characteristics with polyethylene, namely high chemical resistance and low moisture absorption. It also has good fatigue resistance and is suitable for a variety of sterilization methods. As a result, PP is commonly used for components in diagnostic devices, as well as disposable containers for medications and pipettes.
Polyvinyl Chloride (PVC)
PVC is one of the most versatile plastics used in medical devices. It’s known for its good chemical resistance and transparency. Because it can be manufactured to be rigid or flexible, it lends itself well to a wide range of applications, and is used extensively in medical tubing, intravenous tubing, and blood bags.
Polyethylene Terephthalate (PET)
PET is known for its transparency, glossy appearance, and recyclability. As a result it’s a popular choice for implantable medical devices, diagnostic equipment housings, and drug delivery devices, where its biocompatibility and lightweight properties are a big advantage.
Polyurethane (PU)
Like PVC, PU is another of the most versatile plastics used in medical devices. Polyurethane stands out for its hardiness and flexibility, excellent biocompatibility, resilience, and durability. As a result, it is used in a wide range of applications such as catheters, tubing, adhesives, and implantable medical devices like pacemaker leads and cardiovascular devices.
Important Considerations for Medical Device Injection Molding Projects
When taking on a medical device injection molding project, there are a few other factors manufacturers need to consider in relation to material selection.
The first is design flexibility. The chosen materials need to align with the requirements of the end product but they also need to be compatible with the chosen manufacturing method, whether that’s traditional injection molding, two-shot injection molding, or gas-assisted injection molding. Some materials also facilitate a greater flexibility in terms of complex part geometries, while others are more suited to more narrowly defined applications.
Cost considerations are also a major factor when choosing which plastics to use in medical devices. Material cost is determined by things like purity, biocompatibility, and production volume. Some materials might have higher upfront costs but the long-term benefits could outweigh these after a certain point.
And finally, regulatory requirements are a must. Plastics used in medical devices must meet stringent standards put forth by the FDA and EMA in the U.S. Selected materials should undergo biocompatibility testing and validation to meet these standards.
Thogus is a Trusted Injection Molder for Medical Devices
At Thogus, we’ve partnered with healthcare professionals for decades to deliver reliable plastic components for high quality medical devices. We understand the unique demands of the industry and have the expertise to choose the materials that will meet regulatory requirements and meet the demands of your application. But our services don’t end there. From manufacturing by design and material selection to post-production and cleanroom assembly, we’re here to be your injection molding partners from beginning to end.
Contact our team today to get started.
Experience the Thogus Difference
Connect with us today to discuss your project and to learn more about our capabilities.