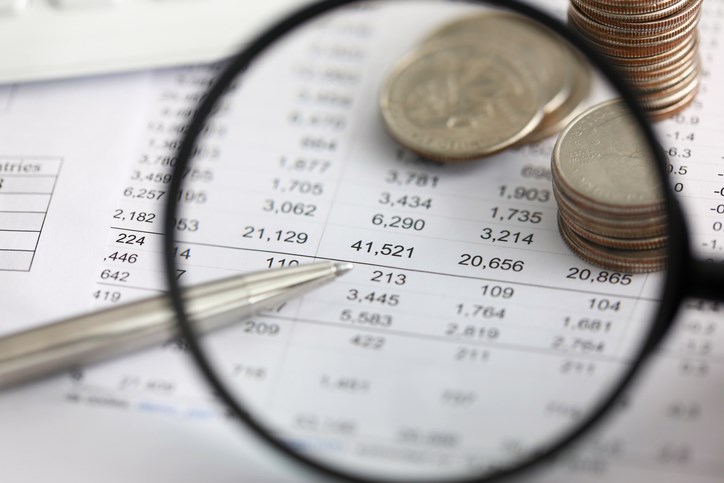
For manufacturers who want to optimize their production processes and ensure project feasibility, it’s essential to understand the cost of injection molding. While often favored for its efficiency and scalability, injection molding does involve a range of costs that can impact overall budgets and decision-making. Fortunately, with insights into these cost factors, manufacturers can make more informed decisions that align with their production goals. Let’s take a closer look at each cost factor in detail.
What Factors into the Cost of Injection Molding?
Several key factors come into play when evaluating the cost of injection molding. Some of the most influential factors include:
- Tooling Costs: Tooling represents one of the most significant costs in injection molding. The complexity of part design, the number of cavities in the mold, the material used, and whether or not your part requires a custom mold all influence tooling costs. However, keep in mind that investing in durable, well-designed molds can lead to long-term savings by reducing the need for repairs and maintenance.
- Material Costs: The choice of material is another major factor. Different resins and compounds have varying price points and the specific properties required for the finished parts often dictate selection. Engineered materials, for instance, may offer enhanced performance but often come at a higher cost.
- Production Costs: Production costs include various operational expenses such as labor, machine time, and energy consumption. The efficiency of the injection molding machine, the complexity of the part design, cycle times, and volume also influence overall production costs — streamlining each of these as much as possible can lead to significant cost reductions.
- Post-Production Costs: Post-production costs encompass the additional processes that are required to finish molded parts (e.g. trimming, assembly, painting, quality inspection, etc.) Each of these processes can add substantial costs depending on what is needed. Implementing efficient techniques and minimizing waste can do a lot to help minimize these expenses.
Volume and Economies of Scale
When it comes to the cost of injection molding, production volume plays a critical role. It’s one of the methods most well-known for economies of scale: as production volumes increase, the cost per unit decreases. In high-volume manufacturing in particular, fixed costs such as tooling and setup are distributed over a larger number of units. This makes the cost per part significantly lower.
However, keep in mind that additional factors — think part complexity, material selection, and cycle time — can influence how costs fluctuate at different volumes. Complex parts that require longer cycle times or specialized materials may experience cost increases that offset some of the savings in this area. But even with that, injection molding remains one of the most cost-effective manufacturing methods for high volumes of plastic components.
How Design Choices Affect the Cost of Injection Molding
In terms of design, making strategic decisions early on in the process can have a significant impact on the cost of injection molding, particularly the costs related to tooling, material usage, and production efficiency.
For instance, Design for Manufacturability (DFM) is the practice of creating part designs that are optimized for the injection molding process. This helps manufacturers engineer components that can be produced efficiently and at lower costs. The simpler the part, the lower the tooling and production costs. Manufacturers can achieve this by reducing the number of undercuts, avoiding sharp corners, and utilizing consistent wall thicknesses, to name a few. These types of design elements also generally increase cycle times. By avoiding them where possible, manufacturers can get through production faster.
Material selection is another major factor, as it is in almost every area. Commodity plastics are usually more affordable, but they may not always deliver in strength and durability. Engineered resins, on the other hand, offer enhanced mechanical properties like heat resistance at a higher cost. However, keep in mind that choosing higher-end materials is often worthwhile (and sometimes non-negotiable) for certain projects. This is particularly the case in industries like automotive, aerospace, and medical, where part performance and reliability outweigh the initial cost.
Hidden Costs of Injection Molding
Factors like tooling, materials, and production expenses are often the focus of calculations for the cost of injection molding. But there are hidden costs that, if not accounted for, can catch manufacturers off guard and lead to unexpected expenses and delays. A few of these include:
- Maintenance and Repairs: Ongoing maintenance is crucial to ensuring the performance of injection molding tooling, especially in high-volume production cycles. Neglecting regular maintenance can result in costly repairs or the need for replacements, which can lead to extended downtime; proactive maintenance, on the other hand, helps prevent unexpected failures and ensures the tool performs as needed.
- Defects and Waste: Defects like warping, sink marks, flash, or incomplete fills can lead to considerable waste in both material and time. Defective parts often need to be reworked or scrapped entirely, which wastes both resin and labor hours. Minimizing defects through precision mold design, material selection, and process optimization is key to reducing waste and keeping costs in check.
- Shipping and Logistics: Shipping and logistics are often overlooked in the cost of injection molding, but these can add up quickly — especially for large, bulky, or fragile parts. Other factors to consider include whether or not parts will require specialized packaging or international transit, both of which can add to the overall cost.
- Regulatory Compliance: Finally, achieving compliance with certifications like ISO 9001 or ISO 13485 often comes with added costs related to documentation, audits, and quality control measures. However, these are essential for maintaining industry credibility, avoiding legal issues, and gaining access to certain markets. As a result, these types of costs are usually already worked in.
Minimizing the Cost of Injection Molding: Strategies and Best Practices
Reducing the cost of injection molding requires a combination of smart design, efficient processes, and strategic decision-making. By focusing on a few key areas, manufacturers can optimize their operations to save money without sacrificing quality:
Efficient Tooling Design
One of the most effective ways to lower injection molding costs is to collaborate early with injection molding engineers to optimize tool designs. Doing this can reduce cycle times, improve part quality, and minimize waste. By optimizing aspects such as gate location, cooling channels, and ejection systems, manufacturers can create tooling that runs more efficiently and reduces overall production costs.
Material Optimization
Choosing the right material is essential to controlling the costs of injection molding. Remember that the higher cost of high-performance material is often offset by benefits like increased durability and faster cycle times, both of which can lead to long-term savings. Conversely, for less demanding applications, lower-cost commodity plastics can be a more economical choice. The key is to select the material that meets the performance requirements of your parts without overspending on unnecessary features.
Using Standard Parts for Molds
Using off-the-shelf mold bases, pins, and other components allows manufacturers to avoid the expense and time associated with custom parts. Standardized components are not only more affordable, but they are also easier to replace or repair, reducing downtime if maintenance is needed. By using standard parts where possible, manufacturers can speed up the mold-building process and reduce overall tooling expenses.
Automated and Advanced Technology
Technologies like molding simulation software can optimize tooling designs and predict potential issues before production even begins. This can result in significant cost savings on trial-and-error adjustments. On top of that, real-time monitoring systems can detect problems during production, which allows for immediate corrections to prevent defects and waste. And automation, including the use of robotics in production, helps streamline processes, reduce labor costs, and improve consistency — especially in high-volume manufacturing.
Outsourcing vs. Domestic Manufacturing
The debate between outsourced vs domestic manufacturing has been going on for several years. The truth is that there are advantages and drawbacks to both. Outsourcing often reduces upfront costs for equipment and facilities, and can provide access to specialized expertise. However, it also usually involves shipping costs, longer lead times, and potentially less control over production quality.
Domestic manufacturing, while generally more costly up front, offers greater control over the process, more flexibility in meeting production schedules, and faster response times to any issues that arise. It’s important to weigh the trade-offs between the two based on project needs, timelines, and budgets.
Get the Most Out of Your Injection Molding with Thogus
At Thogus, we know that managing the cost of injection molding is key to the success of your project. That’s why we offer a full suite of injection molding services designed to streamline production and optimize your budget. From efficient tooling design and material selection to high-volume injection molding and secondary services, we help you reduce costs while maintaining the highest quality standards.
By partnering with us, you gain access to a team of experts who are committed to maximizing efficiency and minimizing waste at every step of the process. Whether it’s through design optimization, material recommendations, or the integration of cutting-edge automation, we ensure your project stays on time and on budget.
If you’re looking for ways to lower your injection molding costs without compromising on quality, we’re here to support you. Contact us today to discuss how we can help with your next project.
Experience the Thogus Difference
Connect with us today to discuss your project and to learn more about our capabilities.