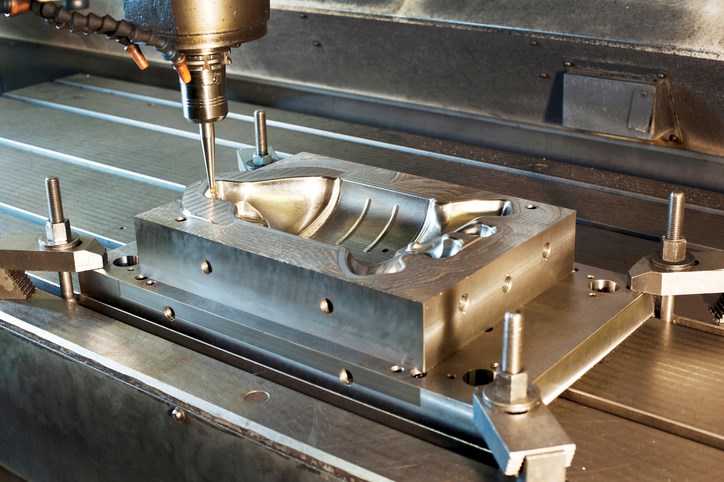
Over the last few months, we’ve touched on the importance of injection molding tooling: its role in complex manufacturing processes and the importance of tooling management. Now, we’re going to take a look at some of the best practices for streamlining tooling manufacturing.
In injection molding, tooling is central to product success. For high-volume production runs and complex parts, tooling must be built to the highest quality standards but also optimized to ensure durability and performance throughout its lifecycle. By employing best practices, manufacturers can streamline their operations. This leads to efficient high-volume production of parts with consistent quality, which in turn helps drive profitability and success.
The Importance of Efficient Injection Molding Tooling Design
Efficient injection molding tooling design is one of the most important factors in optimizing production. A well-designed mold, for instance, can drastically improve production efficiency, reduce cycle times, and enhance the overall quality of the finished parts. On the other hand, poor tooling design can lead to inefficiencies, defects, and costly delays.
Material Selection for Injection Molding Tooling Manufacturing
Few factors matter more in injection molding tooling performance than material selection. Tooling materials directly influence the durability of the mold, the consistency of the parts, how well those parts meet specifications, and the overall production speed.
High-performance tooling materials like pre-hardened steels or alloys, for example, are designed to withstand the stresses of high-volume production, reducing wear and tear over time. As a result manufacturers can maintain consistent part quality, reduce defects, and minimize downtime caused by mold repairs or replacements.
A couple of the most common materials used in tooling include:
- P-20 Pre-Hardened Steel — This material is widely used in injection molding tooling due to its balance between durability and machinability. P-20 offers good toughness, making it ideal for medium- to high-volume production, and its pre-hardened nature reduces the need for additional heat treatment, which saves time and cost.
- Beryllium Copper — Known for its excellent thermal conductivity, beryllium copper is commonly used in areas of the mold where faster cooling is needed. It enhances heat dissipation and speeds up cycle times without compromising part accuracy. This material is particularly useful for molds that require rapid, precise cooling for intricate or high-precision parts.
A quick note on balancing cost and quality: while high-performance materials like pre-hardened steels and beryllium copper come with a higher upfront cost, this is countered by long-term benefits like extended mold life, fewer repairs, and faster production cycles. By investing in higher quality materials from the start, manufacturers can reduce overall costs in the long run by avoiding frequent tool maintenance, part defects, and slowdowns in production.
Leveraging Advanced Manufacturing Technology for Injection Molding Tooling
In recent decades, cutting-edge manufacturing technologies have revolutionized the way injection molding tooling is designed, produced, and maintained. For instance:
- CNC (Computer Numerical Control) machining has long been a cornerstone of tooling manufacturing due to its ability to produce highly accurate and complex molds. With the latest advancements in CNC machining, manufacturers can achieve even tighter tolerances and more intricate geometries.
- 3D printing and other additive manufacturing techniques are becoming increasingly valuable for rapid prototyping and tool creation. These technologies allow for faster development of mold inserts or smaller tooling components without the need for traditional machining processes.
- Real time tooling performance monitoring allows manufacturers to detect any deviations or anomalies in the tooling process, enabling quick adjustments to maintain optimal production conditions.
- Automation and robotics have become indispensable in high-volume injection molding operations. Integrating robotics into tooling manufacturing not only improves production speed but also ensures greater consistency and precision in repetitive tasks.
Injection Molding Tooling Optimization for Improved Efficiency
One of the best ways to optimize injection molding tooling is by leveraging advanced techniques like molding simulation software and flow analysis. These tools allow manufacturers to enhance tooling performance, reduce cycle times, and minimize production costs.
Molding simulation software, for instance, allows manufacturers to virtually test and refine tool designs before production begins. Through these simulations, manufacturers can evaluate material flow, cooling times, pressure distribution, and other critical parameters that influence part quality and cycle time.
Collaboration with Tooling Partners for Successful Production
Finally, early collaboration with manufacturers is one of the best ways to ensure tooling design efficiency. By working closely with tooling engineers from the outset, you can identify potential issues and align tooling design with production goals. This proactive approach helps avoid expensive rework or last-minute adjustments that can cause delays and increase costs.
Ongoing communication between manufacturers and tooling suppliers is also essential for continuous improvement throughout the production lifecycle. Regular feedback loops enable quick adjustments to be made as production progresses.
Thogus’ Commitment to Collaboration in Injection Molding Tooling Design and Manufacturing
At Thogus, collaboration is at the heart of our approach to tooling manufacturing. We recognize the importance of building strong, long-term relationships with our clients and tooling partners to ensure the success of every project. Our team is involved from the very beginning, providing expert guidance and support through each phase of the production lifecycle.
We don’t just focus on tool creation — we also offer ongoing support and continuous improvement throughout the life of the tooling. From initial design consultation and tooling management to maintenance and repair, we’re dedicated to ensuring that your tooling performs at its best for the duration of your project.
That, alongside our extensive injection molding capabilities, material expertise, and dedication to white-glove service enables us to provide you with full end-to-end manufacturing solutions to meet all your needs.
Connect with us today to get started.
Experience the Thogus Difference
Connect with us today to discuss your project and to learn more about our capabilities.