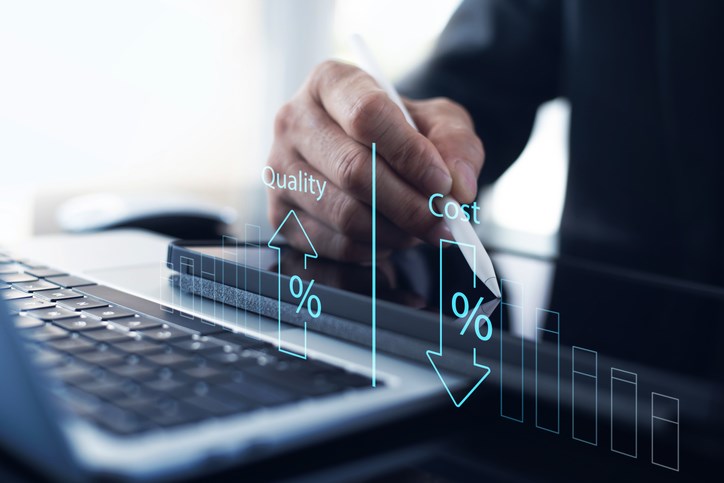
Injection molding is one of the most important modern-day manufacturing methods. It’s one of the only solutions that is versatile, capable of high volumes, and relatively quick once the initial setup is complete. Consequently, it’s important that these services be accessible for a range of industries without sacrificing part quality. But the cost of injection molding can be a significant barrier… unless you’re working with a manufacturer who knows how to achieve injection molding cost reduction. Let’s take a look at how that works and what you can expect from such a partnership.
What are the Costs Associated with Injection Molding?
Unlike other plastic manufacturing methods, injection molding is a relatively complex but extremely efficient process. As a result, there are several factors that contribute to the overall cost of the method. A few of the most prominent include:
- Tooling costs: Tooling costs are often the most significant upfront investment in injection molding. They include the design, fabrication, and testing of molds, which must be highly precise and durable to produce consistent parts over many cycles. Complex molds with intricate features or multi-cavity designs can significantly increase these costs.
- Material costs: Material costs vary depending on the type of plastic used. Commodity resins are less expensive, while engineering and high-performance materials like PEEK or carbon-filled resins are pricier due to their superior properties. The quantity of material required and waste generated during production also contribute to overall material costs.
- Labor costs: Labor costs involve the time and expertise required to set up, operate, and maintain injection molding machines, as well as to monitor and troubleshoot the production process. Highly skilled operators and technicians are essential, especially for complex projects, adding to labor expenses.
- Production costs: Production costs encompass the expenses related to machine operation, including energy consumption, wear and tear, and maintenance. Higher production volumes can reduce per-unit costs, but initial setup and ongoing production can be costly, particularly for complex or low-volume runs.
- Secondary operations: Secondary operations such as assembly, painting, pad printing, sonic welding, or additional machining add to the overall cost. These processes are often necessary to complete or finish the part but require additional labor, equipment, and time.
- Quality control: Quality control costs include the inspection, testing, and validation processes required to ensure parts meet specifications. Advanced quality assurance equipment, such as metrology tools and automated inspection systems, are often necessary, particularly for high-precision or regulated industries, adding to the overall cost.
Injection Molding Cost Reduction Strategies
Part Design Optimization
One of the most effective ways to achieve injection molding cost reduction is through part design optimization. Complex designs often require intricate tooling and longer cycle times, increasing costs. By simplifying the part’s geometry, manufacturers can use more straightforward, less expensive tooling and reduce the time needed for production.
Reducing wall thickness also enables manufacturers to use less material and shorten the production cycle, leading to cost savings. And finally, combining multiple components into a single molded part can reduce assembly time, labor costs, and the number of molds required. This consolidation reduces the overall cost and complexity of the manufacturing process.
Material Selection
When it comes to material selection, fewer things impact the performance and quality of your parts more. But material is also a good place for injection molding cost reduction. For instance, choosing materials that are widely available and less expensive can significantly lower costs while still meeting the necessary performance and regulatory requirements.
There are also several ways that injection molders can optimize material usage during the molding process to minimize excess material that would otherwise go to waste. This can be achieved through precise mold design, efficient process control, and recycling scrap material where possible.
Tooling Cost Management
Tooling is a vital part of injection molding but it can be one of the most expensive parts of the process. Still, a manufacturer may encourage clients to invest in higher-quality tooling as opposed to cheaper options. While they may have a higher upfront cost, better tooling provides enhanced durability and precision, leading to longer tool life and reduced maintenance expenses over time.
Modular tooling also allows for greater flexibility and reuse of parts of the tool across different projects. This reduces the need for entirely new molds for each project, thereby lowering overall tooling costs. And, of course, regular maintenance and repair helps ensure longevity and performance.
Production Efficiency
Fortunately, there are many strategies within production itself that manufacturers can use to achieve injection molding cost. By refining the injection molding process, including fine-tuning machine settings and optimizing cooling times, manufacturers can reduce the overall cycle time per part, leading to faster production rates and lower costs.
Incorporating automated systems and robotics into the production line can also significantly enhance efficiency. Automation can handle repetitive tasks such as part removal, inspection, and packaging, reducing the need for manual labor and minimizing errors.
Leverage Scale of Economies
Finally, one of the biggest advantages of injection molding is that it enables manufacturers to leverage economies of scale, particularly in high-volume runs. Producing larger quantities of parts allows manufacturers to spread the fixed costs, such as tooling and setup, across a greater number of units, thereby reducing the cost per part.
By increasing production volumes, manufacturers can also take advantage of bulk purchasing discounts on materials, reduce machine idle times, and optimize labor utilization, leading to overall cost reductions.
Get Cost-Efficient High Volume Injection Molding Solutions with Thogus
At Thogus, we offer specialized mid- to high-volume injection molding services for key industries, backed by our decades of experience. Our comprehensive range of services includes traditional injection molding, two-shot injection molding, and gas-assisted injection molding, as well as engineering assistance and secondary operations, allowing us to meet the unique demands of your project. We have the expertise, resources, and capability to customize manufacturing solutions to your exact specifications, ensuring fast and accurate production of plastic components.
Interested in exploring the advantages of injection molding for your upcoming production? Contact our team today to begin the process.
Experience the Thogus Difference
Connect with us today to discuss your project and to learn more about our capabilities.