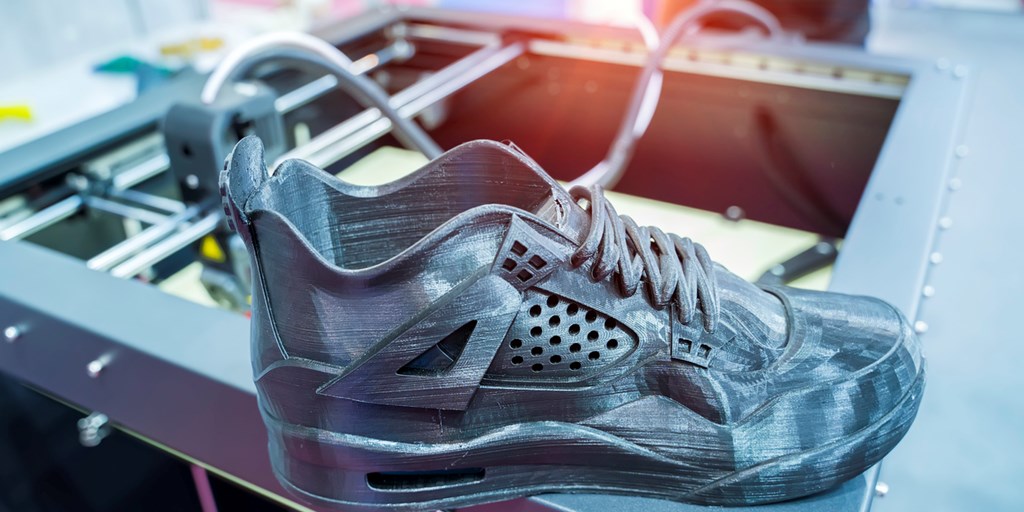
Necessity is the mother of invention, and last year, we’ve found ourselves with plenty of necessity. The COVID-19 crisis, as well as new technologies and global economic conditions, has driven the plastics manufacturing industry to new heights, and we expect even more progress in key areas in the future. Here are five design trends in plastic products to be aware of:
1. Environmentally Friendly Designs
At least 48% of consumers in the United States say they are willing to change their buying habits to be more environmentally friendly. There are many ways to incorporate sustainable elements into consumer products in every stage from material selection to packaging.
One key element in plastics manufacturing is lightweighting, which can be achieved through the use of materials that naturally weigh less than other options, and that can be designed to offer the same strength and durability with less material use. Lightweight options are more environmentally friendly because they require less fuel and packaging to ship. In automotive manufacturing, the environmental benefits are more direct, with lightweighting substantively increasing the fuel economy and decreasing the carbon emissions of consumer vehicles.
2. Automation
Automation is increasing all over the manufacturing industry, and plastic injection molding is no exception. Automation helps ensure accuracy and consistency in product production, in addition to saving time and money. Especially in large volume runs, automation can make the difference between a profitable output that runs on schedule and wasted time or money.
But there’s more to automation than simply plugging in the robots. Manufacturers need to design parts to integrate smoothly with the automation process by considering the touch points between parts and automation machines, the relationship between material selection and automated cooling and tooling times, and secondary operations that need to be incorporated into the automated process.
3. Plastics Design for the Automotive Industry
The market for plastics in automotive design is expected to reach $68.58 billion by 2025 — so it’s safe to say this trend is going strong. In addition to the lightweighting advantages discussed above, plastics are valued in automotive manufacturing for their ability to increase design flexibility and to push technological innovation. From creating sleek, modern lines on vehicle bodies to custom, energy-efficient electric components, the plastics design possibilities in the automotive industry are limitless.
4. High-Performance Materials
Resins can be customized to meet almost any performance needs, so much so that custom resins actually outperform metal alternatives in many scenarios. They’re also more design-flexible and can be adapted to suit most tolerances without sacrificing cost or aesthetics. For that reason, plastic product designs featuring materials that are resistant to corrosion and high temperatures are the next word in innovation.
5. 3D Printing
3D printing is often talked about alongside injection molding in plastics manufacturing, but the two processes offer different benefits. While injection molding is highly customizable and ideal for medium to- high-volume projects, 3D printing has shorter lead times, allows for smaller batches & offers the ability to consolidate multiple parts into one due to the manufacturing process. 3D printing also allows for faster prototyping and design testing, so get ready for increased modifications and iterative designs.
At Thogus, we are constantly staying up to date on best practices, innovative designs and efficient processes to injection mold your plastic parts at the highest level. Contact us today to talk through your project.
Experience the Thogus Difference
Connect with us today to discuss your project and to learn more about our capabilities.