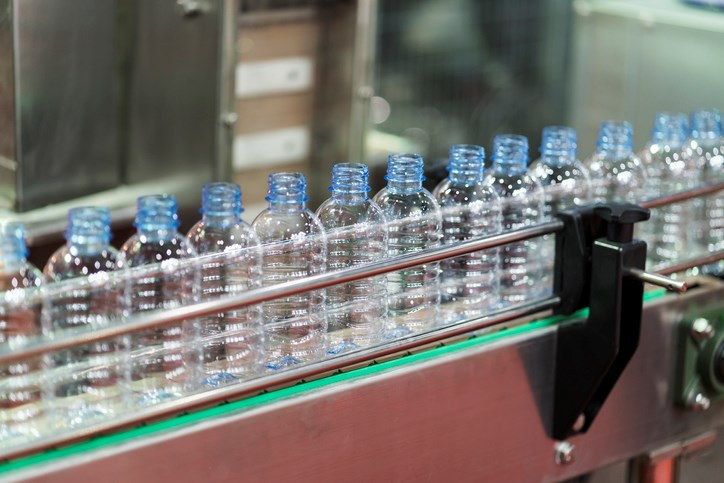
When selecting the right injection molding partner, volume and capacity are two aspects that are likely at top of mind. And, if your project requires large production runs, then you’re probably most interested in working with high volume plastic injection molding experts. High volume plastic injection molding is a common manufacturing solution for a number of industries, including the consumer products, automotive, and plumbing industries.
But how do you know if your project is suitable for high volume injection molding? Here are a few things to think about.
An Ideal High Volume Plastic Injection Molding Project
If you want to determine whether your project is well-suited for high volume plastic injection molding, it’s helpful to have a better understanding of exactly what that looks like.
For instance, a typical high volume project might involve producing plastic caps for beverage bottles. They are standard screw-on caps with a straightforward design, featuring threads for easy closure and a tamper-evident band to ensure product integrity. The material is likely a general or industrial-grade plastic like polyethylene or polypropylene.
Why It’s Ideal For High Volume Production
The production of plastic beverage bottle caps is a project that is uniquely suited to the high volume plastic injection molding process. There are a few different reasons for this, including:
- High quantity demand — high volume injection molding, as the name suggests, is a process that offers fast turnaround on mass quantities of parts.
- Standardized design — injection molding excels in producing large quantities of parts with consistent and uniform designs. The simple design of the bottle caps allows for a streamlined manufacturing process.
- Fast cycle times — with fast cycle times, injection molding enables the rapid production of parts. This is crucial to meeting the demands of the beverage industry.
- Low tooling complexity — The simple design of the caps also contributes to lower tooling complexity, lowering costs and boosting efficiency.
- Scalability — injection molding is extremely scalable, allowing for easy adaptation to changes in market demand.
- Cost-effective per part production — Finally, all of the above contribute to this particular project becoming more cost-effective as volume increases, as the initial cost of set-up can quickly be counterbalanced by the sheer number of parts produced.
High Volume Plastic Injection Molding For Other Projects
Outside of those parameters, high volume plastic injection molding may still be a viable option under other circumstances as well.
For instance, in the case of more complex parts with high demand, the initial investment for tooling and production setup may be higher. However, this elevated cost is often offset by the cost-effectiveness of mass production. This is great news for these types of projects, as injection molding is one of the better solutions for creating intricate geometries and tackling the challenges of complex designs.
For high value parts, it's critical that quality control measures are in place. But as long as they are, high volume plastic injection molding can also be a cost-effective solution for creating mass quantities of high value components while maintaining the integrity and consistency of the parts.
And finally, when one of your priorities is having a stable and reliable supply chain, high volume injection molding is an excellent solution. The repeatability of the process reduces the chances of part variability, and the ability to scale helps ensure you’ll be able to meet demand consistently.
Thogus Specializes in High Volume Plastic Injection Molding
At Thogus, we specialize in high volume injection molding for a wide range of industries, including healthcare, consumer products, electronics, and automotive. Our manufacturing facilities are located in Avon Lake, OH, and are equipped with the latest in advanced manufacturing technology and equipment. We approach every project with a focus on delivering white glove service and meeting your every standard.
Our services also include engineering support, automation, tooling, and secondary operations, so we can provide you with a one-stop plastic manufacturing solution to streamline your production and strengthen your supply chain.
Ready to get started? Connect with our team of experts today.
Experience the Thogus Difference
Connect with us today to discuss your project and to learn more about our capabilities.