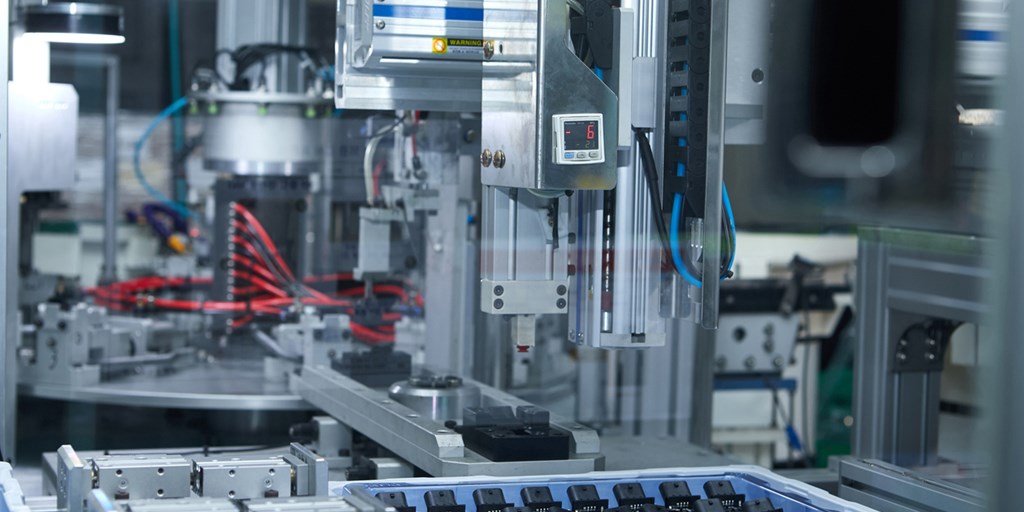
Injection Molding Design Guidelines for Tooling
As industries develop ever increasing needs for precision and performance, injection molding has become one of the go-to methods for the production of plastic components. At the heart of this precision lies tooling, which plays a pivotal role in determining the quality of the final product and the efficiency of the production process. Proper tooling not only influences how well components fit together but it can also impact production timelines and costs. In order to maximize these benefits, manufacturers adhere to a number of injection molding design guidelines for tooling. Let’s take a closer look at those guidelines and how following them enables injection molders to optimize your projects for success.
The Importance of Tooling Design in Injection Molding
The design of tooling is critical to the success of nearly every injection molding project. It directly impacts product quality, production efficiency, and cost-effectiveness. Well-designed molds also ensure tight tolerances and consistent dimensions, which are essential for high-precision applications in industries like automotive and medical devices.
When it comes to production costs, efficient tooling can often reduce cycle times and minimize scrap. It also facilities more flexibility and customization, which enables manufacturers to make quick adjustments to meet market demands. It can also accommodate more complex designs, enhancing product functionality and aesthetics.
Injection Molding Design Guidelines for Tooling
Material Selection
Choosing the right material for the mold is critical. Tooling materials must be able to withstand the high pressures and temperatures associated with injection molding. Common materials for tooling include steel, which offers durability and longevity, and aluminum, which provides a lower-cost option for shorter production runs. The choice a manufacturer makes will impact tool life, cost, and the quality of the final parts.
Part Geometry
Designing the mold to accommodate the part geometry is vital. This includes considering draft angles, wall thickness, and rib design. Draft angles facilitate easy ejection of the part from the mold, while uniform wall thickness reduces the risk of warping and ensures consistent cooling. And ribs should be designed to provide strength without adding excessive material.
Tolerances and Specifications
Defining precise tolerances is crucial for meeting quality standards. Tolerances should be established based on the part's function and the capabilities of the injection molding process. It’s important to balance tight tolerances with manufacturability to avoid unnecessary complications during production.
Gating and Ejection System Design
The design of the gates (the openings through which the molten plastic enters the mold) and ejection systems (mechanisms for removing the finished part) can significantly affect the molding process. Gate location impacts flow and pressure, while an effective ejection system reduces the risk of damaging the part during removal.
Cooling System
An efficient cooling system is vital for controlling cycle times and ensuring uniform part quality. Cooling channels should be strategically placed to maximize heat transfer and minimize hot spots. A well-designed cooling system helps reduce cycle times and improve the dimensional stability of the molded parts.
Practical Tips for Tooling Design
When manufacturers adhere to injection molding design guidelines for tooling, there are a few key principles that typically come into play. These include but may not be limited to:
- Design for Manufacturability—Also known as DFM, this is a set of principles aimed at making products easier and more cost-effective to manufacture. When it comes to injection molding design guidelines for tooling, DFM may involve simplifying the part design, ensuring a uniform wall thickness, and incorporating adequate draft angles to facilitate easier part ejection.
- Material Selection—When focusing on injection molding design guidelines for tooling, choosing the best material is essential. The material of the mold should be able to withstand the expected production volume and material characteristics.
- Tool Maintenance and Durability—It’s also important to implement a regular maintenance schedule to keep the tooling in optimal condition, which helps prevent unexpected downtimes and extends tool life. Designing molds with replaceable components like inserts and wear plates also helps simplify maintenance and repairs.
- Simulation and Testing—Another best practice in injection molding design guidelines for tooling is to utilize simulations and other forms of testing. Mold flow analysis software, for instance, simulates the process to identify potential issues like air traps and weld lines, and optimize the mold design before fabrication.
- Documentation and Standards—Finally, it’s essential to maintain comprehensive documentation and adhere to industry standards. Maintaining detailed documentation of the mold design, including drawings, specifications, and material selections helps in making future modifications and troubleshooting.
Thogus Specializes in High-Volume Injection Molding Supported by Precisely Designed Tooling
At Thogus, we’ve been trusted injection molders since 1950. Our specialty lies in the high-volume production of plastic components for critical applications in industries like medical devices, automotive, consumer goods, plumbing, and more. With our advanced manufacturing facilities and team of highly skilled experts, we have the capabilities to deliver the quality and precision our customers require.
Get in touch today to start with a free quote.
Experience the Thogus Difference
Connect with us today to discuss your project and to learn more about our capabilities.