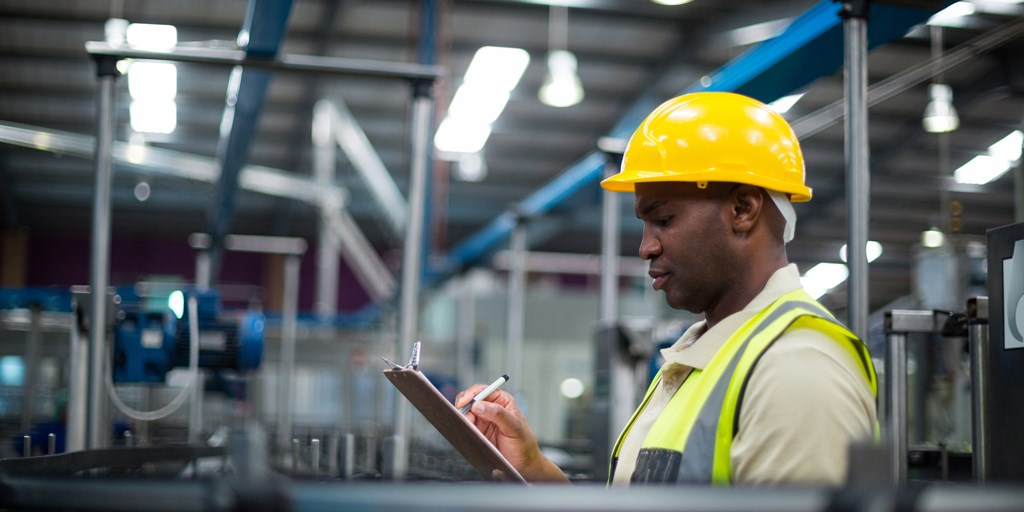
With all of the moving pieces in a project, it’s important to have a functional, detailed checklist to keep you on track. A well-made physical checklist can drastically improve your workflow and keep you organized while making sure that you don’t miss any important steps. Some things are easy for designers and OEMs to forget during the design phase. When you’re thinking big-picture about your product, it is easy to forget how material, part design, tooling and manufacturing requirements interact with each other, leading to delays, cost increases, and production issues. We want to help.
Take control of your new product development process by incorporating the considerations below into your new product development process.
Consideration 1 and 1a: Part Design and Material Selection
What came first, the chicken or the egg? The same question can be asked with part design and material selection. Both are equally important.
- Select the right material – Your material supplier should provide recommendations to help you decide what material is best for your part. Think about physical and mechanical properties as well as the environment your part will need to operate in and make sure you provide all these details to your material supplier so that they can help you make the best choice.
- Wall thickness – Different materials have different parameters regarding wall thickness and transitions. Work closely with the material supplier to ensure your design meets their suggested guidelines. Failing to do so may impact manufacturing, leading to delays and increased costs
- Radii – Does your part have sharp corners? Sharp corners put stress on the walls, so even if you’re using the right materials and have a good handle on your wall thickness, parts with sharp corners can warp. Adding radii to your design takes the stress off the corners and prevents that warping from ruining your part.
- Ribs – By now you’re probably sensing a theme in this checklist — strength is key. Ribs help reinforce the strength of a part without all the problems that come with excessive wall thickness. Just remember, if your ribs add sharp corners, you’ll need to add radii to those too.
Consideration 2: Tooling
The last thing you want to hear is that your product cannot be manufactured as designed.
- Surface appearance – Does your part need a smooth or rough surface? High polish or a matte finish? In other words, what do you want it to look like as part of your finished product?
- Parting lines – A parting line is what we call the seam on a part that’s created where the two halves of the mold meet. All molded parts have one — where do you want the one on your part to be? This can affect the cost of making the mold as well as the appearance of the part, so think about it carefully.
- Undercuts/Recesses/Features – Does your part have holes? Protrusions? Recessed areas? Features like this that create an uneven surface on the part can make it difficult to manufacture the part without proper tooling. Your toolmaker can design the tool to incorporate many features, but your team must be aware of how this impacts quality and manufacturing.
- Gating – Gates come in different sizes and shapes and can be placed in a lot of different locations. Think about where you want the gate for your part to maintain the appearance and structural integrity that you’re looking for.
Consideration 3: Manufacturing
-
Assembly – Do you need an inline or offline assembly process? Manual or automated? Your manufacturing partner should be able to make suggestions based on your needs, so make sure to think about them in advance.
-
Labor and handling requirements – What kind of labor and handling will your manufacturing process require, and have you accounted for these in your budget?
-
Packaging – Does your part need decoration or packaging at the end of the line? If it needs packaging, are you looking for form, function, or both? Document exactly how you want your part to look when it’s delivered.
Consideration 4: Quality Requirements
Setting clear and specific quality requirements ensures that your part is up to snuff when it leaves the manufacturing facility.
- Tolerances – Do your specs allow for some wiggle room, or do you require tight tolerances? Make sure your tolerances meet best practices for the specific manufacturing method.
- Part appearance – Clearly define visual requirements during the design phase, as part design/material, tooling and manufacturing can all impact part appearance and must be accounted for up-front.
- Molding defect acceptance – Sometimes, defects happen. Depending on what they are, you might be OK with the minor ones, they might need to be fixed with some adjustments, or the whole part might be scrap. Decide what molding defects are acceptable versus those that won’t work for your part.
Experience the Thogus Difference
Connect with us today to discuss your project and to learn more about our capabilities.