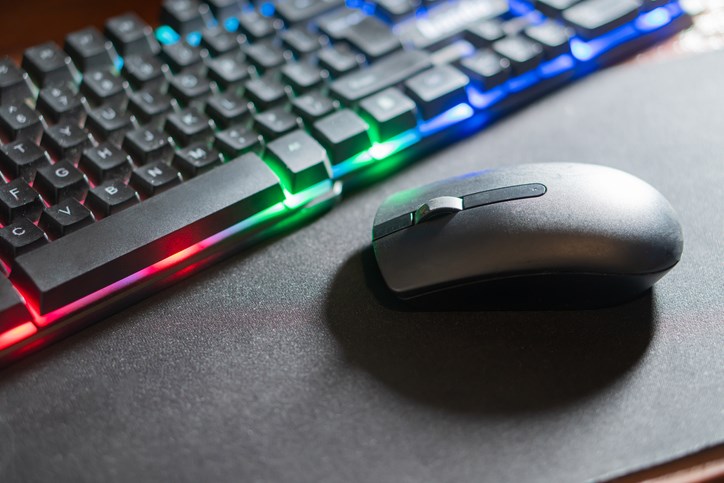
Selecting the right surface finish for your injection molded parts can dramatically impact both form and function. Whether you're developing a medical device that requires pristine cleanliness or an automotive component that needs to withstand daily wear, the finish you choose plays a crucial role in your product's success. Injection molding finishing is a valuable step of the production process, whether it’s to increase the aesthetic appeal of the end product or improve its overall functionality.
But how do you determine which finish is right for optimizing product performance and meeting specific requirements? At Thogus, we’re here to help. Let’s give in to the different injection molding finishing options available and what you need to consider when choosing amongst them.
Types of Injection Molding Finishes
Polished Finishes
This option delivers smooth, glossy surfaces that excel in applications requiring visual appeal or specific functional properties. These finishes are particularly valuable in medical devices where cleanliness is paramount, or in consumer electronics where aesthetic appeal drives market success.
Textured Finishes
These provide practical benefits beyond aesthetics. In automotive interiors, for example, textured surfaces help mask wear patterns and reduce glare, while on tool handles, they enhance grip and user safety. The right texture can transform a basic part into a premium product.
Painted/Coated Finishes
Achieve enhanced protection and customization options with injection molding finishes that involve additional applications of paint or specific coatings. These finishes can provide UV resistance for outdoor applications, color matching for brand consistency, or additional durability for high-wear components.
Metalized Finishes
Metalized finishes create the appearance of metal while maintaining the cost and weight advantages of plastic. Through processes like vacuum metalizing or chrome plating, parts achieve a premium metallic appearance ideal for decorative applications or high-end consumer products.
Specialized Finishes
This option addresses specific performance requirements. Two of the many uses here include anti-static finishes protecting sensitive electronics, and antimicrobial coatings that ensure safety in medical and food packaging applications.
Key Considerations for Selecting the Right Injection Molding Finish
Functional requirements should drive your finish selection. Consider factors like wear resistance, chemical exposure, and temperature requirements. A part that needs to withstand frequent handling requires different surface characteristics than one that remains untouched inside an assembly.
Aesthetic preferences must be balanced with practical considerations. While a high-gloss finish might create an appealing look, it could show fingerprints or scratches more easily than a matte surface. Consider your product's entire lifecycle when making aesthetic decisions.
Environmental factors significantly impact finish performance. UV exposure, temperature fluctuations, and chemical contact can all affect how well a finish maintains its properties over time. Your chosen finish must withstand these challenges throughout the product's intended lifespan.
Material compatibility is crucial for success. Not all finishes work equally well with all resins, and some combinations may require special processing conditions or surface treatments to achieve desired results.
Cost and time efficiency deserve careful consideration. While more complex finishes might offer superior performance, they can impact cycle times and overall production costs. Balance these factors against your product's requirements and market positioning.
The Importance of Collaboration with Your Manufacturer
Early collaboration with your manufacturer is essential for optimal results. At Thogus, our engineering team works closely with clients from the design phase through production, ensuring that injection molding finishing meets both technical requirements and business objectives. This approach sidesteps delays, potential defects, and other quality issues before they become issues.
Prototyping plays a vital role in validating finish selections. Testing different options on prototype parts helps identify potential issues before full production begins, saving time and resources while ensuring quality outcomes.
Get the Right Injection Molding Finish for Your Parts with Expertise from Thogus
Choosing the right injection molding finish requires careful consideration of multiple factors, from functional requirements to aesthetic goals. With decades of experience in custom injection molding, Thogus offers the expertise needed to guide these crucial decisions.
Our commitment to exceptional service means we're invested in your success from initial concept through final production. Let our team help you select and implement the perfect finish for your application. While we’re dedicated to delivering the best in custom injection molding, we also provide a complete suite of secondary operations to give you vertically integrated support. Combined with our extensive material expertise, we find ideal solutions for your injection molding finishing requirements.
Contact Thogus today to discuss your injection molding needs and discover how our finishing services can enhance your product's performance and value.
Experience the Thogus Difference
Connect with us today to discuss your project and to learn more about our capabilities.