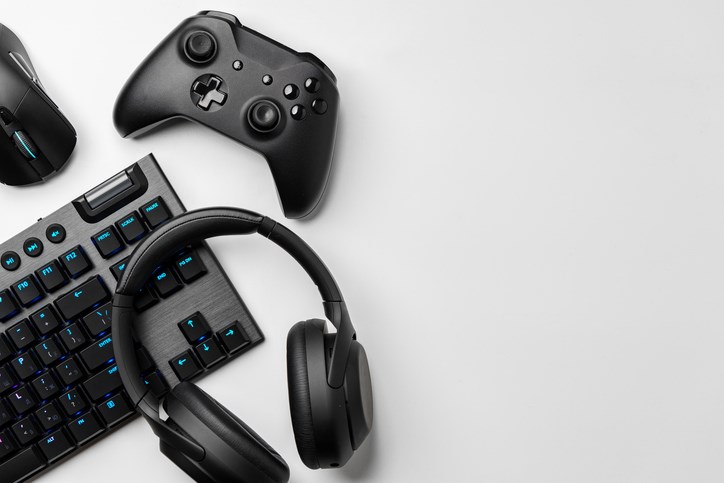
As technology continues to advance (and becomes more integral in daily life), the demand for custom molded electronic components is rising. This is particularly the case in industries that rely on precision-engineered parts that can meet stringent performance standards, such as automotive, medical devices, and consumer electronics. These industries need electronic components that can integrate seamlessly into complex designs and endure rigorous use.
When it comes to the manufacturing of these parts, injection molding is at the forefront. Known for its versatility and efficiency, injection molding enables the creation of reliable, high-quality parts that are essential for today’s sophisticated electronic systems. From intricate housings to durable connectors, injection molding allows for precision and consistency at every stage.
Let’s take a closer look at the development of custom molded electronic components — from initial prototyping to full-scale production — and explore the steps, challenges, and best practices that make it all possible.
The Importance of Prototyping in Electronics Manufacturing
Prototyping is critical to successful electronics manufacturing. It presents the ideal opportunity to test part designs for fit, function, and form before moving into full-scale production. In industries like automotive and medical devices, this stage also helps ensure that custom molded electronic components integrate seamlessly into larger systems and perform as intended.
During this early stage, manufacturers can identify and address potential flaws, and reduce the risk of costly revisions later in the manufacturing process.
At Thogus, we emphasize the role of rapid prototyping in speeding up development timelines without sacrificing quality. By utilizing advanced materials and cutting-edge tooling, we help clients quickly iterate on their designs to achieve the perfect balance of performance and manufacturability. Our rapid prototyping capabilities enable faster time-to-market, allowing you to stay ahead in competitive industries like automotive, medical devices, and consumer electronics.
Selecting the Right Materials for Custom Molded Electronic Components
Alongside prototyping, material selection is another vital part of the development process for custom molded electronic components. The performance, longevity, and quality of the parts are all impacted by the selected polymer. For high-precision parts, for instance, engineered resins often offer the best balance of strength, durability, and performance, making them a preferred choice in industries like medical devices and automotive electronics.
When working with these materials for electronic applications, there are a few considerations to keep in mind. For example, materials must provide excellent electrical insulation to ensure safe operation, withstand heat generated during use, and remain durable under constant wear.
By leveraging our expertise in material selection, Thogus helps clients select polymers that not only meet these requirements but also optimize performance and manufacturability.
Designing for Manufacturability (DFM) for Molded Electronic Components
To create cost-effective and efficient custom molded electronic components, Design by Manufacturability (DFM) principles are invaluable. By prioritizing DFM during the design phase, manufacturers can reduce production costs, minimize waste, and streamline the overall manufacturing process without compromising part quality.
In injection molding, applying DFM principles means optimizing part design for the manufacturing process itself. Features like part geometry, wall thickness, and undercuts significantly influence mold complexity and cycle times. Uniform wall thickness, for instance, reduces the risk of defects like warping, while minimizing undercuts can simplify tooling and accelerate production.
By addressing these factors early, Thogus helps clients avoid costly redesigns and production delays. Our collaborative design approach ensures that every project is guided by the combined expertise of engineers, material specialists, and manufacturing experts. This partnership allows us to fine-tune components for both functionality and manufacturability.
The Transition from Prototyping to Full-Scale Production
Finally, moving from prototyping to full-scale production is a critical phase in manufacturing custom molded electronic components. Scaling requires balancing efficiency with precision while ensuring consistent quality control.
At Thogus, we’re equipped to handle this with state-of-the-art facilities that incorporate automation and real-time monitoring. These tools not only improve production speed but also maintain the consistent quality essential for electronic components. Whether producing thousands or millions of units, our processes are designed to scale without compromising reliability.
Thogus Brings Expertise to Molded Electronic Components
At Thogus, we understand that manufacturing custom electronic components requires more than just technical expertise—it demands a partner committed to your success at every stage of the process. From the earliest design discussions and material selection to prototyping, production, and quality assurance, we’re with you every step of the way.
Our capabilities extend far beyond injection molding. We offer a full suite of services, including rapid prototyping, advanced material expertise, scalable production, and rigorous quality control processes. Our team is dedicated to helping you navigate the complexities of electronics manufacturing with efficiency, precision, and innovation. Whether you’re producing components for automotive systems, medical devices, or consumer electronics, we’re here to ensure your project exceeds expectations.
Ready to bring your custom molded electronic components to life? Contact us today to learn more about how Thogus can support your next project.
Experience the Thogus Difference
Connect with us today to discuss your project and to learn more about our capabilities.