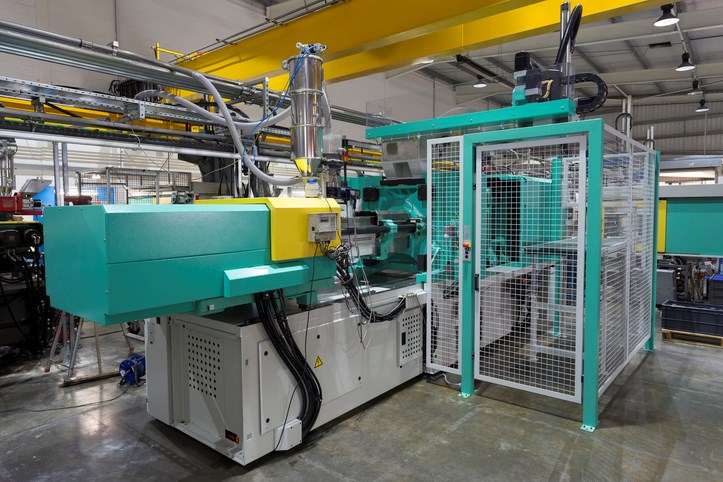
In injection molding, complex molding projects stand out due to the intricate designs, tight tolerances, and specialized materials they often require. Unlike standard molding projects, which may involve simpler geometries and more common materials, complex molding often demands advanced engineering and precision at every stage of the process.
In the first of this three-part series, we’re going to explore the concept of complex molding projects, how manufacturers address the challenges inherent in them, and the role that tooling plays in a successful production run.
What Makes for a Complex Molding Project?
There are several key characteristics that distinguish complex molding projects from more standard production runs. The most prominent ones include
- Intricate part design — Complex projects often involve parts with detailed geometries, undercuts, or thin walls that require precise engineering to ensure they can be molded effectively. These designs call for careful planning and advanced tooling to achieve the desired outcomes without compromising on quality or structural integrity.
- Tight tolerances — For high-volume production, maintaining consistent quality across thousands or millions of parts is crucial. Complex projects often require extremely tight tolerances, particularly in industries like medical or aerospace. Achieving these tolerances ensures that each part functions as intended.
- Use of advanced materials — Advanced materials bring unique challenges, such as higher molding temperatures, greater wear on molds, and the need for specialized equipment. PEEK and carbon-filled resins, for example, offer exceptional strength and thermal stability but require precise control over processing parameters to ensure optimal performance in the final part.
- Complex Mold Design — Molds for complex projects are often multi-cavity, multi-stage, or involve features like hot runners or conformal cooling channels. The complexity of the mold directly impacts the quality, consistency, and cycle time of the parts being produced, making expert mold design a cornerstone of successful high-volume production for complex molding projects.
- Volume requirements — High-volume production amplifies any challenges associated with the molding process. Complex projects require molds and processes that can withstand the demands of producing large quantities without degradation in quality, which necessitates durable materials, robust designs, and efficient production workflows.
- Number of processes involved — Complex molding projects often involve multiple steps beyond basic injection molding, such as overmolding, insert molding, or secondary operations like assembly or finishing. Coordinating these processes requires precise timing and integration to ensure that the final product meets all specifications while maintaining efficiency in production.
How Manufacturers Address the Biggest Challenges of Complex Injection Molded Parts
Part Geometries
Complex part geometries, such as intricate shapes, thin walls, and detailed features, are difficult to mold because they require precise control over material flow, cooling rates, and ejection processes. Achieving uniform filling and avoiding defects like warping, sink marks, or incomplete fills becomes more challenging as the complexity of the geometry increases.
To address this, injection molding experts use sophisticated CAD/CAM software and simulation tools to accurately model and analyze complex part geometries before production begins. Prototyping and iteration is also essential for adjusting and refining designs to ensure they’re optimized for the manufacturing process.
Material Selection
Selecting the right material for complex projects involves balancing numerous factors, including mechanical properties, chemical resistance, temperature stability, and compatibility with other materials. That’s why complex molding projects require experienced injection molders who bring deep knowledge of a wide range of materials. They understand how different materials behave under various conditions, enabling them to recommend the best material for the application, whether it's a high-performance polymer like PEEK or a multi-material assembly.
Precision and Tolerances
Maintaining tight tolerances is crucial in complex projects, especially in industries like medical or aerospace where even small deviations can lead to part failure. Achieving and consistently holding these tolerances throughout high-volume production requires advanced machinery, precise control over process parameters, and real-time monitoring.
To do this, injection molders use high-precision machines capable of holding tight tolerances to ensure that each part is consistent and meets exact specifications. Manufacturers will also incorporate real-time monitoring systems that collect data throughout the production cycle. This data is analyzed to ensure that each part meets the desired tolerances, and any deviations are corrected immediately
Tooling and Mold Design
Designing and manufacturing molds for complex projects can be a challenge because the mold must account for intricate part geometries, specific material behaviors, and high production volumes. Additionally, the mold needs to be durable enough to produce thousands or millions of parts without degrading in quality.
Injection molders work closely with toolmakers to develop molds that are robust, precise, and optimized for efficient production. This includes considering factors like cooling channels, gating systems, and ejection mechanisms that are critical for producing high-quality parts. Regular maintenance also helps ensure integrity and performance are preserved over time.
The Role of Tooling in Complex Molding Projects
Tooling is the foundation for successful complex molding projects. The mold itself is the blueprint for the final part, and its precision directly impacts the accuracy of the molded components. For complex projects requiring tight tolerances, the tooling must be manufactured with extreme precision to ensure that every detail of the part is replicated consistently. Any slight deviation in the mold can result in defects, misalignment, or variations in the final product.
This is even more the case if a component requires complex mold features such as intricate geometries, undercuts, thin walls, and multiple cavities. Tooling must accommodate these features while ensuring proper material flow, cooling, and ejection.
Stay tuned for part two of this blog series, where we’ll cover the manufacturing of tooling for complex molding projects.
We’re Ready to Take on Your Complex Molding Projects
At Thogus, we excel in delivering mid- to high-volume injection molding services across several critical industries. Our extensive capabilities cover injection molding, engineering, post-production secondary services, and quality assurance, ensuring we can handle any project with precision. With the resources, expertise, and capacity to tailor manufacturing solutions to your specific requirements, we’re equipped to optimize your process and deliver high-quality plastic components swiftly.
Ready to harness the power of injection molding for your next production run? Reach out to our team today to get started.
Experience the Thogus Difference
Connect with us today to discuss your project and to learn more about our capabilities.