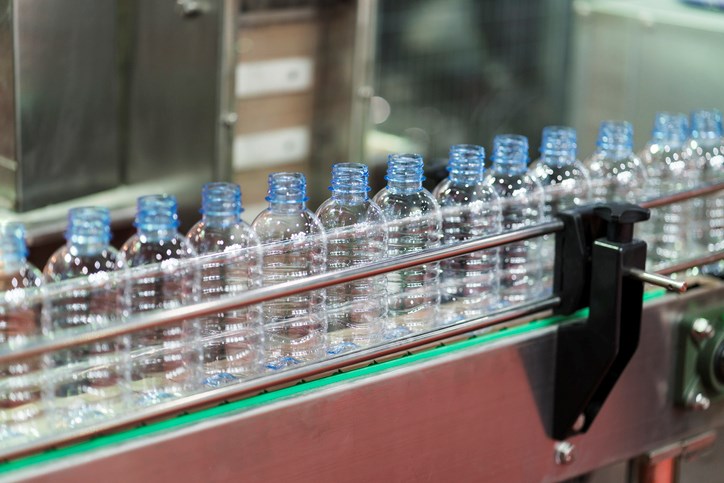
Plastic components have become a central part of everyday life. They’re found in everything from basic consumer appliances and plumbing to automobiles and spacecraft. When it comes to the production of these parts, OEMs have several options available: extrusion, thermoforming, blow molding, and injection molding are a few of the major ones. But how do these types of plastic manufacturing stack up against one another? Let’s take a look.
What are the Most Popular Plastic Manufacturing Methods?
Plastic components perform so many different functions in a variety of industries that a single manufacturing process could never produce them all. For that reason, there are many types of plastic manufacturing. The five most widely used include:
- Injection molding—A process in which molten plastic is injected into a mold cavity under high pressure. Commonly used for complex parts and precision manufacturing.
- Extrusion—In this process, plastic material is forced through a die to create a continuous shape. Typically used for things like pipes, tubing, and sheets.
- Blow molding—Hollow plastic products are formed by inflating a heated plastic tube inside a mold. Best for products like bottles and containers.
- Thermoforming—A process in which a plastic sheet is heated and then molded into a specific shape using a mold. Mostly used for packaging trays, disposable cups, and many automotive components.
- Rotomolding—The formation of hollow products via rotating plastic powder inside a mold to coat the interior. Best for large objects like tanks and playground equipment.
Precision in the Different Types of Plastic Manufacturing
Precision is essential for a number of plastic components, particularly those in which performance and longevity are a concern. Here is what the different types of plastic manufacturing have to offer in terms of precision:
Injection molding: Well suited for creating complex and detailed parts, injection molding is one of the most precise types of plastic manufacturing. Thanks to precision-engineered molds and the high level of control manufacturers have throughout the process, injection molding is capable of producing intricate parts that meet tight tolerances.
Extrusion: Extrusion is best for producing products with consistent cross-sections. It’s a good option for high-volume production but the precision is limited by the complexity of the die. Most suitable for applications where a uniform profile is more important than complex details.
Blow molding: Blow molding offers moderate levels of precision for hollow objects and containers. However, it doesn’t offer the same level of precision as injection molding and tighter tolerances may be more difficult to achieve.
Thermoforming: Best for large, shallow, and simple parts, thermoforming also offers a moderate level of precision for certain applications. However, like blow molding, this precision can be limited and it’s not a good option for parts that require high tolerances.
Rotomolding: Rotomolding offers moderate levels of precision for large, hollow parts where variations like wall thickness is not a major concern. Again, it’s not the best choice if tight tolerances are a necessity.
Versatility in Different Plastic Manufacturing Methods
For some applications, the versatility of the manufacturing method is a non-issue. However, many industries require flexibility for their production. Here is how the different types of plastic manufacturing compare in this aspect.
Injection molding: Along with its precision, injection molding is well-known for being a highly versatile process. This makes it suitable for low- and high-volume production of a wide variety of components.
Extrusion: Extrusion is highly versatile for producing continuous shapes with consistent cross-sections. Again, it’s best for pipes, tubing, sheets, and profiles of varying lengths. It’s not as suitable for 3D or complex products, but is capable of handling various thermoplastics.
Blow molding: Blow molding is particularly well suited for producing large, lightweight, and seamless designs. Within those specifications, it does allow for variations in product size and shape, but is not as versatile as other methods like injection molding.
Thermoforming: Thermoforming is best for producing packaging and disposables, but its use is limited for other applications. Its versatility lies in the different types of materials that can be utilized.
Rotomolding: Best for large, hollow items with low production volumes, rotomolding also has limited versatility in terms of the types of products it can handle. While it can create some intricate details, it’s not the best option for components with tight tolerances.
Production Speed
Finally, one of the biggest considerations when it comes to choosing a plastic manufacturing method is production speed. Let’s take a look at how the different types of plastic manufacturing measure up.
Injection molding: Injection molding is also known for its high production speed, making it one of the fastest plastic manufacturing methods. Cycle times can be relatively short, which allows for the rapid production of large quantities of identical parts.
Extrusion: Extrusion is generally a high-speed process, but this can vary depending on the complexity of the die design and the type of extruded product. However, it’s still a good option for high-volume production of certain products thanks to its efficiency.
Blow molding: Blow molding is a relatively quick process for large-scale production of hollow products. It’s not quite as fast as injection molding for certain applications, but can be an efficient process for large quantities of bottles, containers, and similar items.
Thermoforming: Generally considered a fast process for large, simple shapes, thermoforming has relatively short cycle times and efficiency increases with high-volume production. However, the speed can be impacted by factors like material thickness and part complexity.
Rotomolding: Rotomolding has longer cycle times compared to some other processes, making it one of the slowest methods when it comes to mass production.
The Advantages of Injection Molding
Injection molding is the clear winner when you need complex parts with intricate details and tight tolerances are a major consideration. In most cases, it’s also the best option if you need high-volume production runs with shorter cycle times.
Injection molding is also a highly versatile process. Not only is it capable of producing a wide array of diverse parts, but it is compatible with a long list of materials and generally very cost-effective for mass production.
Experience Excellence in Injection Molding with Thogus
At Thogus, we specialize in high-volume injection molding for a wide range of industries. We’re a manufacturing company that has been around for decades. As a result, we’ve been able to develop our skills and our capabilities to deliver end-to-end solutions, whether you’re looking for material selection support, high-quality injection molding, assembly, and inventory management with JIT deliveries.
Ready to get started? Connect with our team today.
Experience the Thogus Difference
Connect with us today to discuss your project and to learn more about our capabilities.