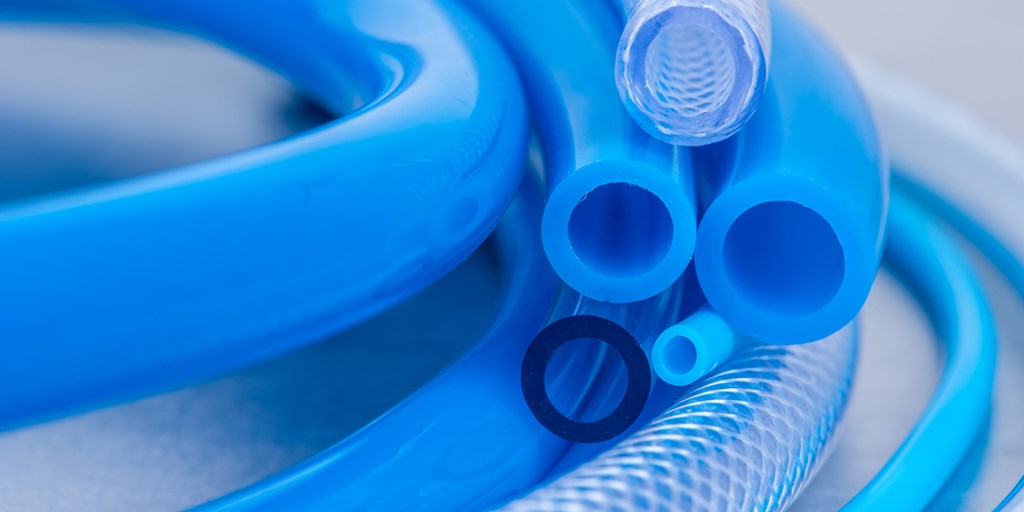
Plastic devices are not new to the medical industry. The original boom of plastics in medical equipment began in the early 2000s and continued to expand over the last 20 years. Now, in 2020, it’s common to see plastic injection molded parts or full devices in hospitals and other patient care and research facilities.
Everything from medical electronics to braces and crutches to tiny pieces like needles and tubing connections can be manufactured with plastic injection molding. Most recently, plastic injection molders were in high demand to help manufacture the ventilators needed to combat the COVID-19 pandemic. With the virus moving quickly and the need for a quick turn around, plastic injection molding for ventilators became the obvious choice over other manufacturing processes.
The benefits of plastic polymers over metals in the medical industry extend beyond times of crisis, though. The cost-effectiveness of plastic injection molding is a day-to-day, bottom-line advantage that can’t be ignored. Part of this money-saving power comes from the fact that plastic is simply less expensive than metal as a material. However, injection molding also has a higher output process than metal machining has. Time is money, so speed and efficiency in manufacturing processes lead to increased savings on entire projects.
Plastic injection molding also provides manufacturers with more options than metal tooling. That’s why delicate medical instrumentals, like scalpels, staplers, and clips used in surgery, are now most often made with plastic polymers. The process of plastic injection molding allows for far more versatility in design, so equipment can be custom-created for specialized procedures, then produced and distributed quickly rather than relying on a “one-size fits all” approach that is necessary for more cumbersome metal parts.
A safer bet
While our brains may not immediately make the association, plastics also provide more safety than metals in medical devices. Part of this is simply due to weight. Healthcare workers physically interact with medical devices all day, every day. When that’s the case, the smallest amount of lightweighting can help combat the fatigue and injuries that are the natural consequences of heavier equipment.
On the other hand, because plastic polymers are so versatile, they can also take the place of heavy metals when the weight is a necessary part of the function. Lead has long been out of favor in the medical industry because of its potential to cause lead poisoning. Unfortunately, even with anti-lead regulations on the rise, there aren’t a lot of alternatives. One alternative that does exist is PolyTungsten, a plastic polymer with a specific gravity of 11 grams per cubic centimeter, the same as lead, making it ideal for blocking radiation in medical settings.
Though this material is notoriously difficult to run; Thogus was one of the first groups to successfully use Poly-tungsten in plastic injection molding. Our unique material expertise prepared us to take on this challenge, along with any others that arise in the fast-moving world of medical device manufacturing.
If you’re interested in reducing costs and improving safety by making the switch to plastic, make sure you talk to an injection molding expert at Thogus from the start of the project. While plastic parts are highly versatile and customizable, our experts can help identify adjustments that need to be made early in the design process.
Experience the Thogus Difference
Connect with us today to discuss your project and to learn more about our capabilities.