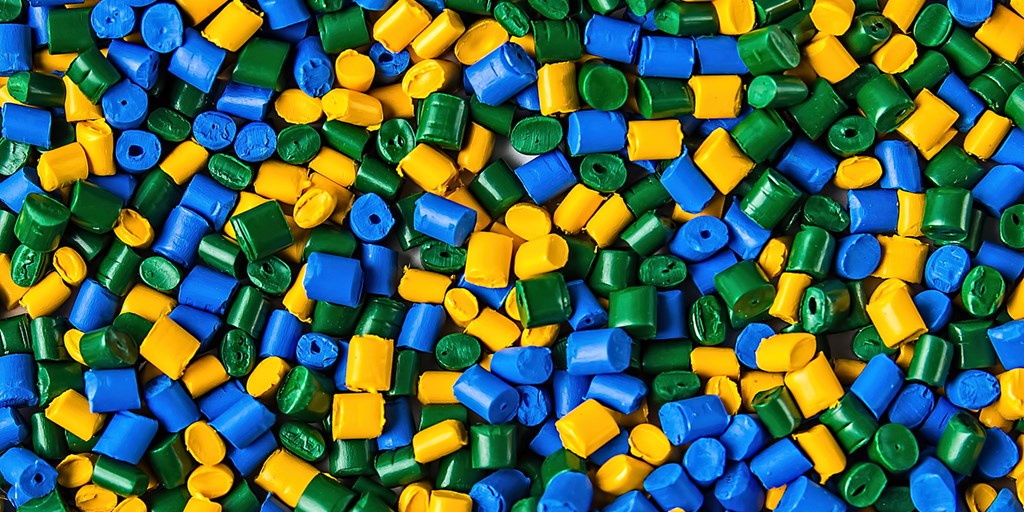
High product markets with high stakes like medical and automotive industries, require precision and attention to detail. Custom plastic injection molding is a good option for markets like this, that have to achieve tight tolerances while maintaining high output and reasonable costs.
Why custom plastic injection molding?
The plastic injection molding process is both robust and repeatable. Custom plastic injection molding allows part design to meet the needs of the product in every way, from custom or commodity resins to unique tooling. The key benefit for parts manufacturers, though, is the ratio of cost to production output that comes with the plastic injection molding process. While the startup costs of plastic injection molding may be slightly higher than, say, machine tooling, the production costs are significantly lower. Injection molding is also optimized for achieving very tight tolerances while maintaining high output.
Plan for tight tolerances from the start
To achieve tight tolerances, parts designers need a good plan for designing and launching their products. That’s why it’s essential for product designers and manufacturers to plan for tight tolerances from the very beginning. Achieving tight tolerances takes the perfect combination of part design, tool design, material selection, and tooling strategy, and upfront planning makes all the difference. A manufacturing by design process can help designers think through their needs for a tight-tolerance part.
Your APQP should determine acceptable and realistic tolerances. As the designer, you’ll need to be specific about tolerances, deviations, and ranges to ensure that you and your manufacturing partner are on the same page. Once you’ve identified and communicated your end goal, your custom plastic injection molder should be able to help develop a plan that’s designed to meet your needs.
Keep it simple (or not)
Complex part designs can be especially vulnerable to shrinking and warping, throwing off your tolerances. That doesn’t mean that a complex design won’t work for a tight-tolerance part — in fact, complex designs can help control tight tolerances when used effectively. The expertise of your injection molding partner is key when you’re working through complexity issues. They can help you predict how the material will behave during manufacturing, including mold heating and cooling as well as shrinkage and warpage. Mid- to high-volume injection molders work with materials and design processes for output often enough that they can help you anticipate problems with tolerances before they arise.
Choose the right materials
The environment that a part will operate in makes all the difference in how the material will behave. Some resins expand or contract in extreme temperatures, others may warp or become brittle. Consider using an engineered resin that is tailor-made to suit your needs. The end results of commodity resins may have more variability from lot to lot, so while it’s possible to use a commodity resin and still achieve tight tolerances, you need a manufacturing partner who understands how the material is going to process.
Choose the right manufacturer
Thogus has experience helping customers achieve tight tolerances in a wide breadth of industries and using many different resins to achieve the kinds of tight tolerances needed for high-quality products. We’re specialists in pushing the capability limits of part design, material and process to repeatedly achieve a stringent outcome.
Contact us today to talk through your project with one of our experts.
Experience the Thogus Difference
Connect with us today to discuss your project and to learn more about our capabilities.