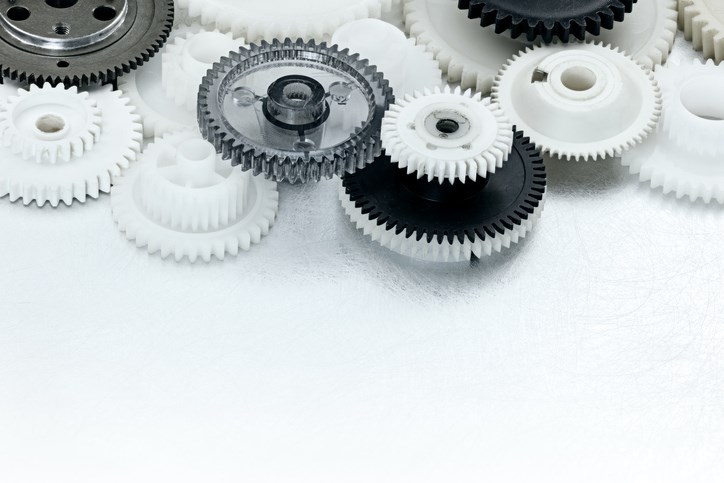
Most critical industries turn to injection molding for their plastic components needs. But when you require critical medical components, automotive parts, or intricate electronic housings, even the smallest dimensional variations can impact functionality, performance, and regulatory compliance. That’s where the importance of injection molded plastic tolerances comes in.
Tolerances can impact everything from part fit and reliability to performance and longevity; maintaining tolerances requires careful consideration of things like material properties, mold design, and process control.
Let’s take a closer look at injection molded plastic tolerances, the challenges involved, and the solutions manufacturers use to meet exacting specifications.
What Are Tight Tolerances in Injection Molding?
Injection molded plastic tolerances refer to the allowable variations in a part’s dimensions from its original design specifications. These variations (often measured in thousandths of an inch or microns) are crucial to ensuring consistency and reliability in production.
Standard tolerances typically allow for minor dimensional variations. Tight tolerances, on the other hand, require far greater levels of precision. Achieving these tight tolerances is particularly important in industries like medical, automotive, and electronics, where even the smallest inaccuracy can lead to product failure.
Several factors influence how well a molded part maintains tight tolerances. A few of the more significant ones include material selection, part design, tooling quality, and process control techniques.
Common Challenges in Achieving Tight Tolerances
Achieving tight plastic injection molded tolerances involves overcoming several key challenges, each of which can impact the final product's accuracy and performance. A few of the most common include:
- Material Shrinkage and Variability — Different resin types have unique shrinkage characteristics, meaning that materials like ABS, polypropylene, and PEEK each behave differently during the molding process. This shrinkage needs to be carefully accounted for, especially for parts with tight tolerances.
- Complex Part Geometries — Intricate designs with small features, thin walls, and tight corners present significant challenges in molding. Uneven cooling rates across these complex geometries can lead to warping or dimensional distortions. Ensuring uniform cooling throughout the part is crucial for maintaining precise tolerances, especially in complex or multi-featured designs.
- Tooling Limitations — High-quality, precise tooling is vital for achieving tight tolerances. Worn or poorly designed molds can introduce inaccuracies and affect the final part's dimensions. Even slight imperfections in tooling can magnify in the molding process, making it difficult to meet exact specifications. Investment in precision tooling and regular maintenance are key to minimizing tooling-related issues.
- Processing Parameters — The molding process itself — particularly temperature, pressure, and cycle times — directly impacts part accuracy. Fluctuations in temperature during molding can cause uneven material flow or inconsistent cooling, leading to dimensional variations. Inconsistent pressure may result in incomplete fills or uneven packing, while incorrect cycle times can either lead to defects or fail to solidify the part correctly.
- Quality Control and Inspection — Advanced quality control methods, such as 3D scanning and Coordinate Measuring Machines (CMM), are crucial for detecting any deviations from tight tolerances during production. These systems enable real-time feedback, allowing manufacturers to identify and address issues early, preventing defects and ensuring quality throughout the process. Effective inspection practices help maintain high standards and reduce the risk of tolerance-related failures.
Proven Solutions for Achieving Tight Tolerances
Optimizing Part and Tooling Design
Achieving tight plastic injection molded tolerances starts with careful part and tooling design. Advanced CAD software and simulation tools enable manufacturers to refine designs before moving to production. These tools enable designers to visualize how the part will behave during the molding process, helping to optimize key features for precision.
When it comes to part design, elements like draft angles, wall thickness, and material flow are also crucial in maintaining accuracy. Proper draft angles, for example, help with part ejection, reducing stress and potential deformation, which is essential for tight tolerances. Maintaining uniform wall thickness throughout the part ensures consistent cooling and minimizes warping. And optimizing material flow helps prevent defects like sink marks and voids, ensuring the final part meets exact specifications.
By integrating these design best practices into the initial stages of production, manufacturers can minimize errors and streamline the process, setting the stage for successful molding with tight tolerances.
Material Selection and Testing
Selecting the right resin is a critical step in achieving tight tolerances in injection molding. Different materials have unique properties, including varying shrinkage rates, thermal expansion, and viscosity, all of which can affect dimensional accuracy. To ensure consistent quality, it's important to choose resins that exhibit predictable shrinkage and stability throughout the molding process.
Testing materials under real-world conditions is also key to ensuring reliability. By subjecting the selected material to temperature changes, pressure variations, and stress tests, manufacturers can assess how it will perform in actual use. This helps to identify potential issues early, ensuring that the final product meets not only the required tolerances but also the performance standards for the intended application.
Scientific Injection Molding Principles
Scientific injection molding relies on precise control over every aspect of the molding process to minimize variability and ensure consistent results. By using process control techniques such as real-time monitoring of temperature, pressure, and flow rate, manufacturers can detect deviations early and adjust as needed, minimizing the risk of dimensional inconsistencies that would impact tight tolerances.
High-Precision Tooling
Investing in high-precision tooling is critical for achieving tight plastic injection molded tolerances. Advanced tooling, including high-quality molds and specialized equipment, provides the necessary precision to produce parts that meet the stringent requirements of industries like automotive, medical, and electronics. By ensuring that every tool and mold is designed and manufactured with exceptional accuracy, manufacturers can consistently produce parts with minimal deviation from specifications.
In addition to initial precision, regular maintenance of tooling is vital to ensure long-term accuracy. Over time, molds and tools can experience wear and tear, which can affect their ability to maintain tight tolerances. Implementing a proactive maintenance program helps identify potential issues before they impact production, ensuring that tools are calibrated correctly and kept in optimal working condition.
Rigorous Quality Assurance
Finally, achieving and maintaining tight plastic injection molded tolerances requires a robust quality assurance (QA) program. Incorporating advanced metrology tools, such as coordinate measuring machines (CMM), laser scanners, and optical comparators, enables precise measurement of molded parts to ensure they conform to the specified tolerances. These tools are essential for detecting even the slightest dimensional variations that could affect the part's functionality or performance.
In addition to metrology tools, in-line inspection systems are crucial for monitoring the production process in real-time. These systems can continuously check parts as they are being molded, identifying defects or deviations from the desired specifications during the production cycle. This helps prevent defective parts from moving further down the line, reducing scrap and rework costs.
Statistical process control (SPC) also plays a key role in maintaining tight tolerances. By analyzing data collected from the production process, SPC allows manufacturers to monitor trends and identify any variations in real-time. This enables data-driven adjustments to be made during production, minimizing fluctuations and ensuring that the molding process remains within the desired tolerance limits.
Experience Our Approach to Tight Tolerance Molding
At Thogus, we pride ourselves on our ability to consistently deliver high-precision injection molded parts, even under the most demanding tolerances. With over 60 years of experience in the industry, we have developed a deep understanding of the challenges involved in tight tolerance molding and the solutions required to meet them.
Our comprehensive approach includes not only optimizing part and tooling design but also selecting the right materials, employing data-backed molding principles, and maintaining rigorous quality assurance protocols. Whether you are in the medical, industrial, or electronics industry, Thogus has the expertise and resources to help you achieve your precision molding goals.
Ready to experience the difference that precision molding can make for your business? Contact us today to discuss your project.
Experience the Thogus Difference
Connect with us today to discuss your project and to learn more about our capabilities.