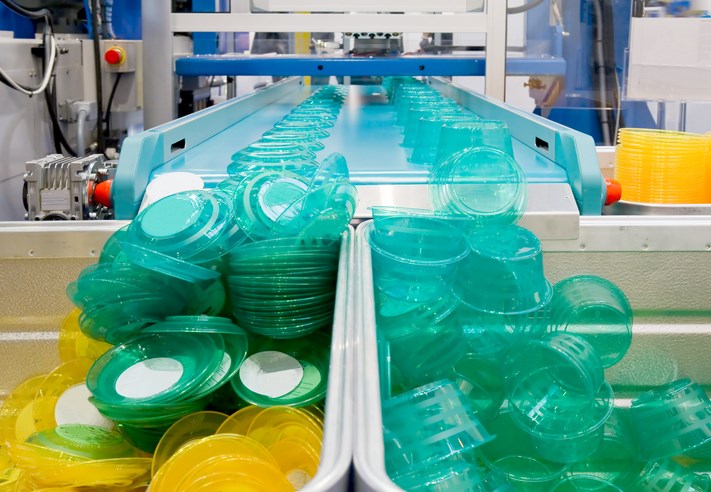
Injection molding is one of the most versatile and utilized manufacturing processes available. When it comes to producing high-quality plastic parts for critical applications, injection molding works well for low- to high-volume production runs. However, high-volume production in particular takes full advantage of all the benefits of injection molding. Let’s explore why injection molding is the go-to solution for those who need high-volume production runs for their plastic components.
The 5 Advantages of Injection Molding for High-Volume Production
1: High-Efficiency and Productivity
One of the biggest advantages of injection molding is that it’s a highly efficient and productive process. In recent years, this is partly thanks to the high levels of automation manufacturers have been able to integrate. Today, machines handle most of the operations, from feeding raw materials to ejecting finished parts. This reduces the need for manual intervention, reducing labor costs and optimizing productivity.
Beyond that, once setup is complete, injection molding involves relatively short cycle times, which enables the rapid production of identical parts. This, combined with the automation and the ability to produce multiple parts per cycle results in a high throughput. All of that results in reduced lead times, making injection molding a go-to method for industries that require quick turnaround times and large quantities of parts.
2: Cost-Effectiveness and Scalability
The second major advantage of injection molding for high-volume production is its cost-effectiveness and scalability. In injection molding, as the number of parts produced increases, the fixed costs (such as mold creation and setup) are spread over more units, reducing the cost per part. This ability to efficiently produce large quantities contributes to significant economies of scale, making the process increasingly cost-effective as production scales up.
On top of that, injection molding is one of the most material efficient means of producing high quality plastic components. Not only does the precision of the method minimize waste, but the waste that is produced, such as sprues, runners, and scrap can often be recycled to reduce costs.
3: Complex Geometry and Design Flexibility
Complex geometries and design flexibility are significant injection molding advantages. Because of the high levels of precision, injection molding is capable of producing highly complicated parts with intricate details. This not only helps maintain quality and consistency, but also opens the door for the creation of custom products that meet a customer’s specific needs.
Injection molding is also ideal for producing parts with high dimensional accuracy and tight tolerances. This is critical when parts must fit together precisely or meet strict performance standards. This accuracy is maintained throughout large-scale production runs, ensuring uniformity and reliability.
4: Consistency and Precision
Injection molding excels in providing consistency and precision for the production of plastic parts. Because of the high levels of control and automation, it’s a process capable of producing parts that are consistent in size, shape, and quality. This is the case even in large-volume production runs, where maintaining quality and uniformity across thousands or millions of parts is critical.
5: Reduced Lead Times
Reduced lead times in injection molding are a significant advantage that allows manufacturers to accelerate production and bring products to market faster. Again, once the initial setup is complete, injection molding is a relatively fast process. Even tooling fabrication and production setup are faster for injection molding than some other methods; this is especially true for standard molds and established processes.
The quick setup and efficient production capabilities of injection molding allow for faster time-to-market. This is crucial for companies looking to launch new products and gain a competitive edge.
Thogus Specializes in High-Volume Injection Molding Solutions
At Thogus, we specialize in mid- to high-volume injection molding services for a number of critical industries. Our capabilities include traditional injection molding, two-shot injection molding, and gas-assisted injection molding. Whatever your project, we have the capacity, the capabilities, and the resources to deliver manufacturing solutions customized to fit your exact needs. Our decades of experience enable us to optimize your process and produce plastic components quickly and accurately.
Are you interested in leveraging the benefits of injection molding for your next production run? Get in touch with our team today to get started.
Experience the Thogus Difference
Connect with us today to discuss your project and to learn more about our capabilities.